In the manufacture of automobile bodies, some components are assembled from the inner and outer panels by crimping and pressing to increase the overall rigidity and strength of the components. Such as the body four doors, hood, trunk lid (collectively referred to as four doors and two covers) and a few models of the top cover, fuel tank flaps and wheel covers. Basically, the outer surface parts of the automobile body are mostly, and the dimensional accuracy and surface quality are relatively high. Therefore, the quality of the edging is directly related to the appearance quality of the whole vehicle and the assembly quality of the whole vehicle. H7 is a new generation of red flag sedan. As a leader of domestic independent brands, it is brave to explore and practice, overcome the difficult problems of the edge-bonding process, and has extraordinary historical significance for product quality improvement.
1. Large angle flanging size is stable
The press-fit of the press and the press-fit of the special machine have higher requirements on the flanging angle of the stamped single piece. Under the premise of ensuring the surface quality after forming, it should generally be controlled below 105. The local corner can be enlarged to 110. This brings difficulties to the stamping of single-piece parts. If the angle of the flanging is increased, not only will the stamping cost be reduced, but also the quality of the forming of the single-piece parts will be reliably guaranteed. However, according to literature research, the pre-flanging angle is greater than 65. Apparent wrinkles appear, and a sharp crimping occurs when the final cuff angle is greater than 56°. If the inner surface is wrinkled, it will cause the outer plate to wave, so a large one-time bending angle indicates that the quality is worse.
The H7 red flag sedan adopts the piping robot to press the edge wrapping technology, and the piping program is set to three passes. Taking the trunk lid as an example, the flange of the part is first folded from 125° to 75° to 90°. Pre-wrapped one time; then fold it from 75° to 90° to 30° to 45° for the second pass, and finally fold from 30° to 45° to 0°. The three-pass edging, also known as the final edging, avoids the problem of hem and wrinkles caused by the hem angle. However, the larger the angle of the flange is, the shorter the arc length of the bend is, and the more difficult it is to control the edge of the edge after the edging, the quality of the part is unpredictable, as shown in Figure 1.
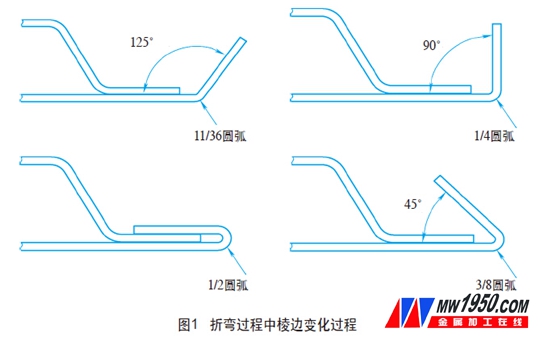
When the workpiece is at 125°, the edge arc length is only 11/36 arc of the entire circumference, until the end of the final hem is 1/2 arc, and the theoretical elongation of the flange length is 63.6%. The degree of difficulty in forming. H7 red flag car parts have strict quality requirements and high dimensional control requirements. After three bends, the size expansion should be less than 0.7mm, and the dimensional parallel difference should be controlled within 0.5mm.
According to the coordinate system of the workpiece, several important measurement points are selected to study the dimensional changes of the different parts of the workpiece. Figure 2 shows the relationship between the amount of change in the contour size of different parts and the position. The ordinate is the amount of expansion and the abscissa is the number of parts measured. The measurement position is as shown in Fig. 3Y to the coordinate number corresponding to the five position points of the assembly.
It can be seen from Fig. 2 that the size variation of the five position points after three times of rolling is not the same, and the five position points have corresponding fluctuations, but the fluctuation amount is controlled within the range of 0.5 mm, which ensures the stability of the workpiece size. .
2. Evening pressure is even
The finished hemming and pressing workpiece is evaluated and measured according to whether the thickness of the pressing edge is qualified, whether the pressing angle is qualified, whether there is wave on the pressing side, whether there is indentation, crack and part size measurement on the surface of the workpiece. Wait. Among them, the surface wave is a common problem that all the edge wrapping processes will appear, and it is also a problem that is relatively difficult to solve. The detecting means can grind the surrounding surface of the part by grinding the stone to reveal a continuous bright and dark area ("bright" part). It is the grindstone area, and the “dark†part is the unpolished area of ​​the grindstone) (see Figure 4).
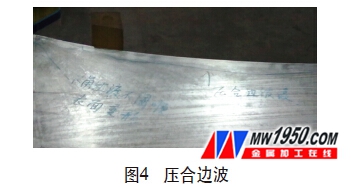
Rolling trajectory and edge pressure are the main factors that generate surface waves. Modern rolling trajectory programs are simulated by simulation software (such as ROBCAD), and then the robot TCP point (ToolCenterPoint) is corrected to realize the roll trajectory operation control. If the accuracy of the TCP point is not high or the quality of the simulation is poor, the robot trajectory will deviate from the theoretical position, the rolling trajectory will travel like a wavy line, and the plate material will be unevenly stressed to form a wave. The H7 red flag car uses ABB robotic piping head cylinders for pressure supply. The control components such as proportional valves are used for pressure control. The pressure is applied to the rollers. The friction between the rollers and the workpiece is used to turn the flanges of the workpiece reserved in the punching direction. Folding, to achieve the edge press, as shown in Figure 5.
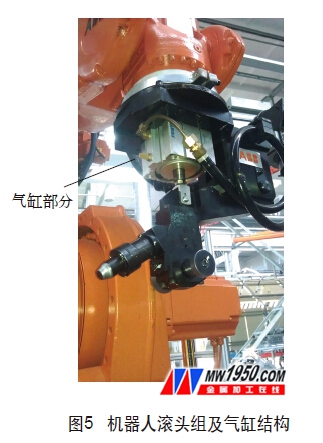
According to repeated commissioning verification, when the thickness of the outer plate is 0.75mm, there are three kinds of piping parameters: the first pass pre-flanging and the second pass pre-flanging are set at 1.5~1.6kN, and the third pass is finished. Set at 1.8~2.0kN (see Figure 6).
The shape is complex or the angular position can be set to a pressure value of 0.6 kN. The value is input into the control system. If the pressure range exceeds 2.0kN, the electronic control unit of the servo proportional valve will alarm the signal, and the robot will stop running to ensure the controllability of the pressure, thus realizing the control of the surface quality of the workpiece.
In addition, the rolling speed is not negligible on the surface quality of the workpiece. The rolling speed per unit time is greater than the deformation stress release rate of the workpiece, which will cause waves on the surface of the workpiece. The flat edge of the H7 red flag car is 200~300mm/s, and the corner or shape is adjusted according to the actual quality after pressing.
3. Innovative rolling head shape
Wang Liying and others of Tongji University proposed that the roller structure has an important influence on the forming quality of the workpiece. The shape of the roller should be rationally designed according to the structure of the workpiece and simulated and verified. Figure 7 shows the H7 red flag car door parts, the buckle has a great impact on the quality of the piping: the buckle is flattened after the piping, and can not play the role of fixed water cutting. Straight edges create surface waves. In order to solve the rolling problem, the car company boldly reformed the roller, and the intermediate car has an annular groove. When the flange is pre-flanged, the buckle just passes through the groove without rolling deformation (see Figure 7 and Figure 8).
After the improved roller head, the buckle can complete the positioning of the water cutting strip and firmly fix the water cutting strip.
4. Conclusion
Although this article lists the improvement methods for the surface quality defects of the parts, it is necessary to analyze and judge according to the actual situation due to the structure and plate of different models. The determination of the specific pressing process should proceed from the actual situation and fully consider the influence factors. In this regard, we will conduct further process research. The author would like to use this article to inspire the jade, and lead experts to think more deeply about the edge-bonding.
About the author: Pan Yuanan, Li Wei, Xie Yuewen, Chen Hongyu, FAW Car Co., Ltd.
PU Rod is divided into polyester and polyether. Polyether Pu Rod is superior to polyester type in terms of resilience, evaporability, low temperature performance, impact strength, heat accumulation, water resistance and mold resistance.Low viscosity and easy operation.Polyester PU rod has high viscosity and difficult operation, but mechanical strength, tensile strength, tear strength, sliding friction, oil resistance, heat aging, metal adhesion, solvent resistance and oxidation resistance are better than polyether PU rod.
PU rod is widely used in metallurgy, mining, petroleum, building materials, cushions, blocks, springs, suitable for all kinds of metal pipe punching die, reducing the friction of general mechanical equipment, buffering shock absorption, is ideal Mold spring.
Product
|
Diameter(mm)
|
Length(mm)
|
Color
|
Density(g/cm³)
|
PU ROD
|
20-200
|
1000
|
nature/tea color
|
1.15
|
16-350
|
300/500
|
PU Rod
Pu Rod ,Extruded Pp Rod ,Polyurethane Rod,Polyurethane Rubber Rod
Shenzhen Anheda Plastic Products Co.,Ltd , https://www.ahdplastic.com