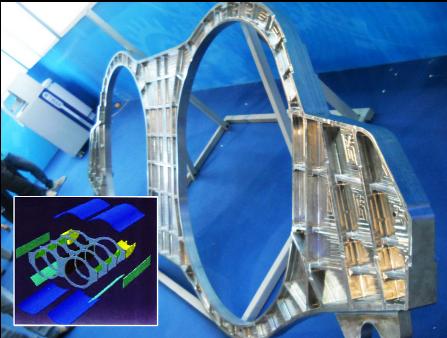
According to the personnel of the material processing engineering of Beihang University who participated in the research, Beihang University has established AVIC Laser with AVIC to realize the industrialization of this technological achievement. At this exhibition, large-scale titanium alloy parts of certain fighter aircrafts were also publicly demonstrated for the first time. The laser integral forming technology of the aircraft's titanium large-scale integral key component is the high-end development of the “3D printing technology†and is a “transformative†short-cycle, low-cost, digital advanced manufacturing technology. For the first time in the world, the project has broken through the laser forming process, mechanical performance control, complete set of equipment and technical standards for the aircraft's large titanium main bearing structure. The large-scale complex key metal parts of more than 30 kinds of titanium alloy lamps have been directly laser-produced and installed in large-scale transport aircrafts, carrier-based aircrafts, C9*** passenger planes, fighter planes and other 7-type aircrafts to solve the bottleneck of model development and make China become a The only country in the world that has mastered laser direct manufacturing technology for high-performance large-scale metal parts and has achieved engineering applications.
There are four laser-enhanced "glass-type" titanium alloy main bearing structural reinforcement frames. What is even more gratifying is that in terms of performance, according to published materials, China has been able to produce laser-shaped titanium alloy components that are superior to the United States. It has become the only country in the world that has mastered the manufacture and implementation of large-sized main bearing elements for laser-shaping titanium alloys.
The laser titanium alloy forming technology completely solves this series of problems. Due to the superposition technology, it saves 90% of the very expensive raw materials, and it does not need to manufacture special molds. The original processing cost equivalent to the material cost is 1 to 2 times. Only the original 10% is needed. Processing 1 tons of titanium alloy complex structure, rough estimate, the cost of the traditional process is about 25 million yuan, while the cost of laser 3D welding rapid prototyping technology is only about 1.3 million, the cost is only 5% of the traditional process. What's more, many complex structures of titanium alloys can be integrally molded by 3D printing, which not only saves man-hours but also greatly increases material strength. Titanium alloy forgings from F-22, if manufactured using China's 3D printing technology, can be reduced in weight by up to 40% with comparable strength.
Door Accessories,Glass Door Closer,Industrial Door Closer,Door Hardware
Caesar door control co.,ltd , http://www.caesar-door.com