Low-density polyethylene (LDPE) is a plastic material that is suitable for various molding processes in thermoplastic molding processes and has good moldability. LDPE is mainly used as a film product, and is also used in injection molding products, medical appliances, pharmaceutical and food packaging materials, blow molding hollow molded products, and the like.
The biggest market for LDPE is the production of films. The single and composite LDPE films produced by the blow molding or casting process account for more than 55% of the total domestic consumption of LDPE. Films made from LDPE exhibit good optical properties, strength, flexibility, sealing, and slow odor diffusivity and chemical stability. LDPE is used to package bread, agricultural products, fast food, textiles, durable consumer goods and some industrial products. LDPE can also be used as a non-packaging film such as disposable diapers, agricultural films and shrink films.
Squeeze the glue. It is another major market for LDPE. Due to the structural characteristics of the LDPE molecule, it is the only resin in the family of polyethylene resins that can meet the requirements of the extrusion coating process. The adhesive provides a protective layer that helps seal the finished package, with excellent tensile properties, long-lasting coverage and low odor diffusing. Typical melt indices range from 3 to 15 grams per 1 minute.
LDPE adhesives can be applied to many substrates such as paper, board, fabric and other polymeric materials. LDPE coating is an economical and effective means to ensure the heat sealing and moisture resistance of the substrate. The market for LDPE toppings is a milky box, sterile antiseptic package, food packaging, tape and paper products.
LDPE coextrusion is widely used as a component of high barrier composite laminates. The important requirements are moisture protection and sealing. The performance of the resin will vary depending on the requirements. It can be used for aseptic packaging, packaging of pharmaceuticals and daily necessities, and molding. In the competition of the polyethylene resin family, blow molding and injection molding have been relatively stable using conventional LDPE, and LDPE resin has been used for molding due to its flexural resistance and processing characteristics.
Bushing Cover For Surge Arrestor comes out because of The exposed and live parts of the electricity must be insulated to ensure the safe operation of maintenance personnel, and at the same time to prevent animals from climbing to the live parts and causing short circuits and malfunctions.
The existing lightning arrester Insulation Protection Cover is directly wrapped on the metal head of the arrester, and the two bent sides are locked by the buckle so that the protection cover is tightly hugged on the metal head of the arrester. However, because the existing lightning arrester is not transparent, it should When the instantaneous discharge produces black smoke, the maintenance personnel cannot detect it. You need to remove the protective cover and check whether there is black smoke attached to the inner wall of the protective cover to judge. However, because the buckle is locked and then removed, the buckle cannot be locked again. The protective cover is hug tightly on the metal head of the arrester, the installation is no longer firm, and it is easy to slip off, which is easy to form a safety hazard.
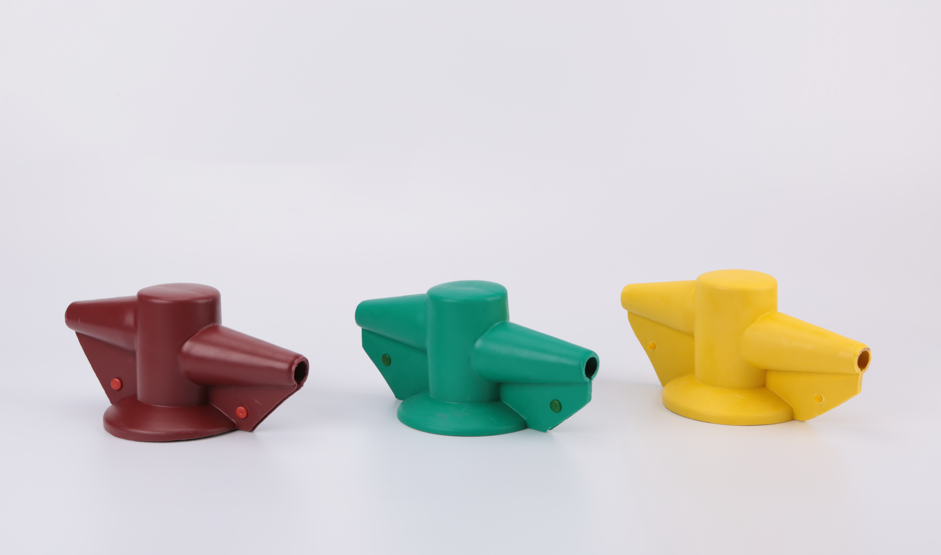
Bushing Cover For Surge Arrestor
Customized Bushing Cover ,Insulation Protection Cover,Insulating Enhancement For Surge Arrester,Insulation Protection For Surge Arrester
ShenZhen FUJI Electric Material Co., Ltd , https://www.sinofuji.com