Types and Characteristics of Hydraulic Seals
Hydraulic seals play a crucial role in preventing leaks in hydraulic and pneumatic systems. Poor sealing can lead to uncontrolled external leakage, which not only contaminates the environment but also allows air and dust to enter the system. This can negatively affect the performance and smooth operation of actuators, causing issues like crawling or inconsistent movement. In severe cases, it may reduce the volumetric efficiency of the system, making it impossible to achieve the required working pressure. On the other hand, over-sealing can cause excessive wear on the sealing components, shorten their lifespan, increase friction, and lower the overall mechanical efficiency of the system. Therefore, selecting and designing an appropriate sealing solution is essential in the development of reliable hydraulic and pneumatic systems.
First, the Requirements for Hydraulic Seals
1. A good hydraulic seal should maintain effective sealing under various working pressures and temperatures, and ideally, its sealing ability should improve automatically as the pressure increases.
2. The seal should have minimal friction with moving parts and maintain a stable coefficient of friction.
3. It must be resistant to corrosion, aging, and wear, and should have some self-compensation capability after wear.
4. The design should be simple, easy to install and maintain, and cost-effective.
Second, the Types and Features of Hydraulic Sealing Devices
Hydraulic seals can be classified into two main categories based on their working principle: non-contact seals and contact seals. Non-contact seals rely on small gaps between mating surfaces, while contact seals use direct physical contact to prevent leakage.
1. Clearance Seal
A clearance seal uses a small gap between moving parts to block fluid flow. It is commonly used in cylindrical joints such as those found in pistons, plungers, and valves. Some valve plugs feature pressure equalizing grooves on their outer surfaces, which help distribute radial pressure evenly, reduce hydraulic clamping force, and minimize leakage. However, this type of seal cannot compensate for wear over time and is typically used in low-diameter applications, such as in hydraulic pumps or spool valves.
2. O-Ring
O-rings are made from oil-resistant rubber and have a circular cross-section. They provide excellent sealing performance by sealing on both inner and outer sides as well as the end face. Their compact design reduces friction on moving parts, making them easy to manufacture, assemble, and disassemble. O-rings are widely used in hydraulic systems due to their versatility across different pressure levels. The groove design for O-rings can vary, including rectangular, V-shaped, dovetail, semi-circular, and triangular shapes, and should be selected according to standards and manuals.
3. Lip Seal
Lip seals come in various shapes, such as Y-shaped, V-shaped, U-shaped, and L-shaped. Under hydraulic pressure, the lips of the seal press against the surface of the mating parts, creating a dynamic seal that adjusts automatically with pressure changes. Higher pressure results in tighter sealing, while lower pressure reduces the lip's contact force, minimizing friction and power loss. Additionally, lip seals can self-compensate for wear, maintaining consistent sealing performance. To ensure proper function, the lip opening should face the pressure side so that the seal adheres tightly to the surface.
4. Combined Sealing Device
As hydraulic technology advances, the demand for more reliable and long-lasting seals increases. Single sealing rings often fail to meet these requirements, leading to the development of combined sealing devices. These devices combine multiple elements, such as rubber seals and support rings, offering high reliability, low friction, and significantly extended service life—up to 100 times longer than standard rubber seals. They are widely used in engineering applications where performance and durability are critical.
5. Shaft Sealing Devices
There are various types of seals designed for rotating shafts, primarily used in hydraulic pumps, motors, and rotary cylinders to prevent oil leakage from the housing. These seals are essential for maintaining system integrity and reducing maintenance needs.
6. Adhesive Sealing
Adhesive sealing involves applying a sealant to the joint surface, creating a bond that prevents fluid leakage. Another method, tape sealing, uses a sealing tape wrapped around threaded connections to fill gaps and prevent seepage. Both methods are practical solutions for certain sealing applications.
[Sealing gasket, metal winding gasket, metal coated gasket, ladle gasket, stainless steel gasket, copper gasket]
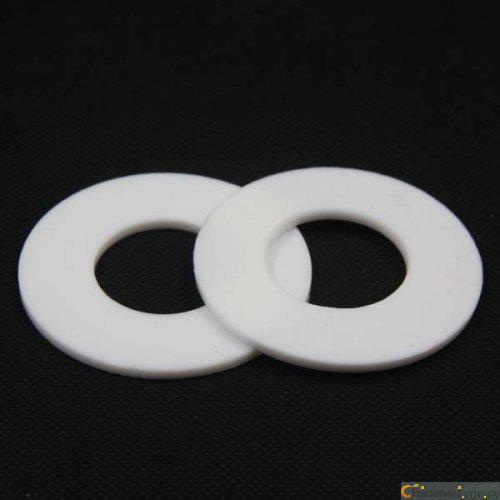
Hydraulic seals play a crucial role in preventing leaks in hydraulic and pneumatic systems. Poor sealing can lead to uncontrolled external leakage, which not only contaminates the environment but also allows air and dust to enter the system. This can negatively affect the performance and smooth operation of actuators, causing issues like crawling or inconsistent movement. In severe cases, it may reduce the volumetric efficiency of the system, making it impossible to achieve the required working pressure. On the other hand, over-sealing can cause excessive wear on the sealing components, shorten their lifespan, increase friction, and lower the overall mechanical efficiency of the system. Therefore, selecting and designing an appropriate sealing solution is essential in the development of reliable hydraulic and pneumatic systems.
First, the Requirements for Hydraulic Seals
1. A good hydraulic seal should maintain effective sealing under various working pressures and temperatures, and ideally, its sealing ability should improve automatically as the pressure increases.
2. The seal should have minimal friction with moving parts and maintain a stable coefficient of friction.
3. It must be resistant to corrosion, aging, and wear, and should have some self-compensation capability after wear.
4. The design should be simple, easy to install and maintain, and cost-effective.
Second, the Types and Features of Hydraulic Sealing Devices
Hydraulic seals can be classified into two main categories based on their working principle: non-contact seals and contact seals. Non-contact seals rely on small gaps between mating surfaces, while contact seals use direct physical contact to prevent leakage.
1. Clearance Seal
A clearance seal uses a small gap between moving parts to block fluid flow. It is commonly used in cylindrical joints such as those found in pistons, plungers, and valves. Some valve plugs feature pressure equalizing grooves on their outer surfaces, which help distribute radial pressure evenly, reduce hydraulic clamping force, and minimize leakage. However, this type of seal cannot compensate for wear over time and is typically used in low-diameter applications, such as in hydraulic pumps or spool valves.
2. O-Ring
O-rings are made from oil-resistant rubber and have a circular cross-section. They provide excellent sealing performance by sealing on both inner and outer sides as well as the end face. Their compact design reduces friction on moving parts, making them easy to manufacture, assemble, and disassemble. O-rings are widely used in hydraulic systems due to their versatility across different pressure levels. The groove design for O-rings can vary, including rectangular, V-shaped, dovetail, semi-circular, and triangular shapes, and should be selected according to standards and manuals.
3. Lip Seal
Lip seals come in various shapes, such as Y-shaped, V-shaped, U-shaped, and L-shaped. Under hydraulic pressure, the lips of the seal press against the surface of the mating parts, creating a dynamic seal that adjusts automatically with pressure changes. Higher pressure results in tighter sealing, while lower pressure reduces the lip's contact force, minimizing friction and power loss. Additionally, lip seals can self-compensate for wear, maintaining consistent sealing performance. To ensure proper function, the lip opening should face the pressure side so that the seal adheres tightly to the surface.
4. Combined Sealing Device
As hydraulic technology advances, the demand for more reliable and long-lasting seals increases. Single sealing rings often fail to meet these requirements, leading to the development of combined sealing devices. These devices combine multiple elements, such as rubber seals and support rings, offering high reliability, low friction, and significantly extended service life—up to 100 times longer than standard rubber seals. They are widely used in engineering applications where performance and durability are critical.
5. Shaft Sealing Devices
There are various types of seals designed for rotating shafts, primarily used in hydraulic pumps, motors, and rotary cylinders to prevent oil leakage from the housing. These seals are essential for maintaining system integrity and reducing maintenance needs.
6. Adhesive Sealing
Adhesive sealing involves applying a sealant to the joint surface, creating a bond that prevents fluid leakage. Another method, tape sealing, uses a sealing tape wrapped around threaded connections to fill gaps and prevent seepage. Both methods are practical solutions for certain sealing applications.
[Sealing gasket, metal winding gasket, metal coated gasket, ladle gasket, stainless steel gasket, copper gasket]
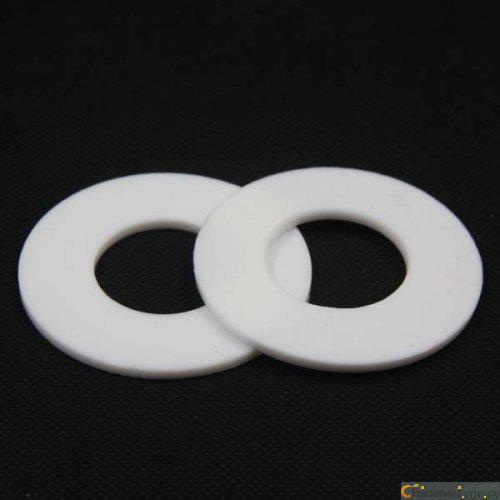
KMP Cat Parts,Cat Engine Parts,KMP Cat Stamping Parts,Custom KMP Cat Parts,CAT Spare Parts
JINING SHANTE SONGZHENG CONSTRUCTION MACHINERY CO.LTD , https://www.stszcmparts.com