High energy consumption, low material utilization rate, serious pollution, and low economic efficiency have constrained the development of the foundry industry. Therefore, energy conservation and material conservation has become one of the most important issues in the healthy development of China's foundry industry.
The foundry industry is a major energy consumer in the manufacturing industry, so there is a great potential for energy savings. High energy consumption, low material utilization rate, serious pollution, and low economic efficiency have restricted the development of the foundry industry. Therefore, rational use of energy and materials has become one of the most important issues in the healthy development of China's foundry industry. Now we will briefly introduce the energy-saving material technology and process of our company in the production of large-scale castings, and share it with the founding colleagues.
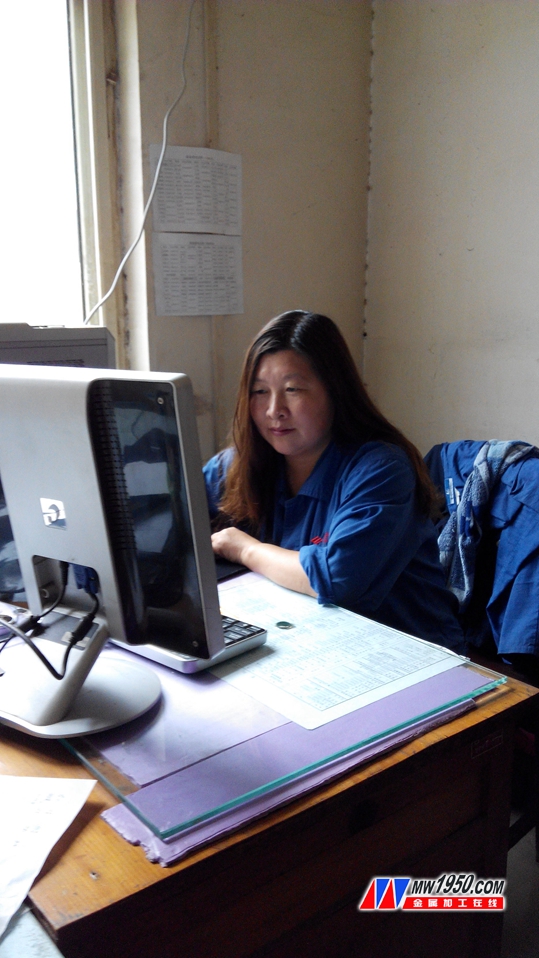
Ji Yunling, senior engineer of Jigang Group Heavy Industry Machinery Co., Ltd.
Simulation technology and internal and external cold iron applications
It is well known that if the process of the thick steel castings is unreasonable during the casting process, the improper setting of the pouring riser may cause defects such as shrinkage and shrinkage. Applying computer simulation technology in the casting process to predict casting defects such as shrinkage and shrinkage in castings can assist process optimization, guide the actual production of castings, reduce the scrap rate of castings, and improve the quality of castings. Through the optimization design of the casting system, the largest Limit the material utilization rate, reduce the mass ratio of the riser and increase the process yield. For example: our company used the simulation technology in the production of the exporter crusher connecting rod (see Figure 1), and reasonably designed the inner and outer cold iron, and achieved good results.
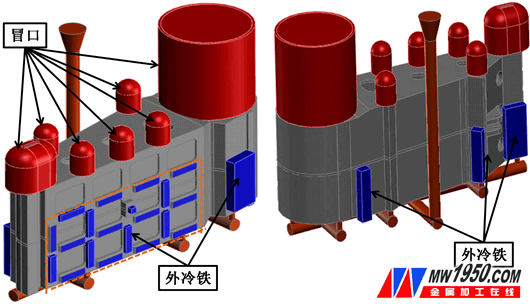
Figure 1 Simulation of connecting rod riser and external cold iron
Through the simulation analysis and the placement of the inner and outer cold irons, the defects of the castings are reduced, the process yield of the castings is improved, and the raw materials are saved.
Polyethylene foam application
For some large-scale single-piece castings, if the ordinary wood mold is used, the cost is high and the production is difficult. The use of foam plastic wood mold can significantly reduce the production cost and improve labor efficiency. In addition, the application in a specific part can also reduce the cost and improve the yield of castings. For example, the slag tank support shaft is a difficult point in slag casting because of the strict dimensional accuracy requirements. Our factory adopts the following measures in production: the whole support shaft is treated as a live block, the support shaft is made of forgings, and the cone part combined with the tank body is made of polyethylene foam plastic, and the shaft head is used as an embedded part to be combined after polyethylene foaming. Inside the entire fulcrum, a threaded hole is drilled in advance on the shaft head to be combined with the can body. After the styling is completed, the bolt is taken out. In order to further position the shaft head, the shaft head is fixed by bolts on the sand box, then the bubble is burned clean with gas, the residue is blown off with compressed air, and the core is used to secure the shaft from the inside, thereby solving the branch. The problem that the dimensional accuracy of the shaft is not easily ensured reduces the scrap rate caused by this factor. as shown in picture 2.
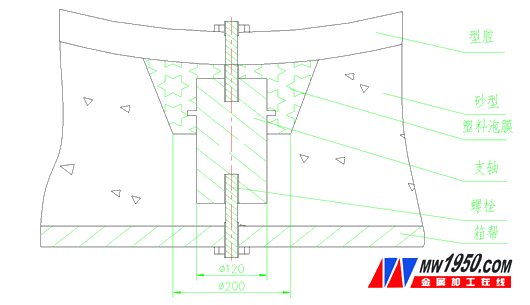
figure 2
Application of lost mode
In today's casting process, the lost foam process is a relatively advanced new process, the castings are precise in size and shape, the surface roughness value is low, and there is no flash burr; the casting defects caused by the mold taking and the box are eliminated; the molding sand preparation department is cancelled. And waste sand treatment process; can significantly reduce the machining allowance of castings, improve the production rate of the process, and has a great effect on the energy-saving materials of enterprises. The lost foam model replaces the traditional sand casting, and at the same time realizes the cast state of the ductile iron, which can save the heat treatment step with a large amount of energy consumption, and the energy saving effect is obvious. Figure 3 shows the application of the lost foam process in our company's production of furnaces. Through the production of the lost mold, the dimensional accuracy has been improved from the original 13 to 10 to 11, and the processing volume has been reduced from 20 mm to 10 mm. The cost of modeling has been reduced from 2,500 yuan / t to 500 yuan / t, labor efficiency has doubled, and the production rate has increased from 65% to 95%.
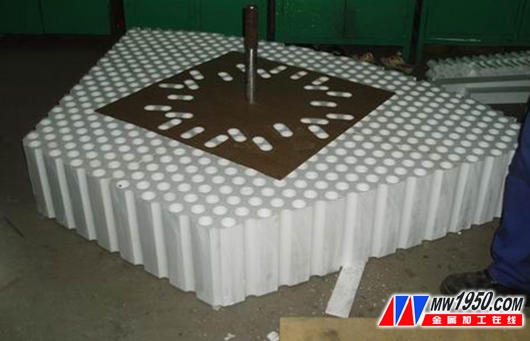
Figure 3 furnace scorpion lost mode
In addition, our factory added coke to the sand core of some large castings, which not only can improve the permeability of the sand core, but also reduce the amount of core sand, which greatly reduces the cost of casting materials.
The energy-saving materials in the foundry industry are fundamentally based on improving the quality of castings, reducing the rate of scrap and reducing consumption, using computer technology applications, selecting new materials, and adopting advanced technologies and equipment as the main means of comprehensive energy-saving materials.
Ultrafine Silica Median Particle Size 2~4
Ultrafine Silica Median Particle Size 2~4,Silicon Oxide Powder,Silicon Carbide Powder,Silicon Dioxide Powder
Changxing Wanxing Building Material Co., Ltd. , https://www.wxbuildingmaterials.com