Cable fault tester features use knowledge lecture |
One. Overview: Power transmission is an important link in the power supply system. In recent years, due to the acceleration of urban construction and the need for safe power supply, more and more buried cables and channel cables have been widely used in urban and rural power facilities. Cables have the following advantages over overhead lines: 1. The floor space is small, and the underground laying does not occupy the floor space. It can avoid setting poles and wires on the ground, which is conducive to safety and beautiful appearance. 2. It is reliable in operation and is not affected by the external environment. It can avoid short-circuit and grounding faults caused by windstorms, floods, kites and birds. 3. The personal safety is reliable, and underground laying can effectively avoid personal electric shock caused by line breakage. 4. The large capacity of the cable is conducive to improving the power factor of the power grid. It is precisely because of the above reasons that cables have been widely used in the construction of modern cities. However, because the cable is buried underground, and some transmission cables are still relatively long (several kilometers), when the power cable fails and affects the normal power supply, it also brings certain difficulties to find the cable fault point. The main reason is that the cable is buried underground, invisible, intangible, and sometimes more difficult to handle when the cable is not laid. In the past, it was often a few days or ten days to find a cable failure point without advanced test equipment. And it will cause an incalculable loss of power outage. Therefore, the search for cable faults is one of the important issues that have been plaguing the power supply sector for many years. two. Analysis of the cause of cable failure: There are many reasons for the failure of the power cable, but the main causes of the failure are as follows: 1. Mechanical damage: Many faults are caused by careless installation of the cable or near construction work near the cable. Sometimes, if the damage is not serious, it will take several months or even a few years for the damage of the damaged part to develop into the perforated lead skin, and the intrusion of moisture will cause the damage to completely collapse. 2. Electrical corrosion of the cable sheath: If the power cable is buried under the ground with a strong underground electric field (such as a large-scale aerial vehicle, near the track of an electric locomotive), the lead sheath of the cable is often corroded and caused to cause moisture intrusion and insulation damage. 3. Chemical Corrosion: If the cable path passes through an acid or alkaline area, the benzene vapor of the gas station often causes cable armor and lead skin to be corroded over a large area and over a long distance. 4. Subsidence: This phenomenon often occurs when cables pass through roads, railways, forest areas, and buildings. The cable is vertically deformed due to the sinking of the ground and the growth of the roots. Causes various types of failures caused by cable armor, lead damage, and even breakage. 5. Loss of cable insulation: when the cable is laid, the ground groove is uneven, or the outdoor head is on the pole. Due to the undulation of the cable and the difference between the height and the low, the insulation oil of the high-rise cable flows to a low place, so that the insulation performance of the cable at a high place is lowered. Causes a failure to occur. 6. Long-term over-load operation: Due to the overload operation, the temperature of the cable will rise. Especially in the hot summer, the temperature rise of the cable often leads to the breakdown of the cable first, which is the reason for the cable failure in summer. 7. Vibration damage: The cable running under the railway track, due to the intense regular movement, causes the cable skin to be elastically fatigued and ruptured, forming a fault. 8. Poor mechanics: Poor joints and cables that are not technically required are often the main cause of cable failure. 9. In the case of wet weathering, the joint is filled with water vapor and can not withstand the test voltage, often forming a flashover fault. 10. External force damage: In recent years, due to urban construction and construction, the use of large-scale construction machinery, and the construction workers did not understand the underground conditions of the construction site, the power cable was cut off or dug. In the analysis of the cause of the cable failure, it is very important to pay special attention to the situation in the cable laying. If the cable appearance is suspicious, you should check the correct record after the cable installation work is completed. These records should include Details: the cross-sectional area of ​​the copper or aluminum core cable, the insulation method, the exact position of each joint, the direction of the cable path, the condition of a cable to another cable or joint in an underground relationship (this should be specially noted) And the precise position of the cable to the connector with two different cross-sectional areas: whether there is abnormal laying depth or special protection measures, such as steel plate, pipe, and pipe; the name of the technician in the cable laying (these people) It is one of the sources that provide important source material; and a detailed record of the failure of the cable (place and exclusion). All of this information is important when you want to quickly locate a fault. Cable failures due to manufacturing defects are rare. Thus, the analysis of cable faults, if considered in the above circumstances and details, will give cable repair technicians tremendous benefits. three. Pulse test principle: A few basic concepts: Transmission characteristics of power cables in high-frequency applications: During the transmission of high-frequency waves, the parameters such as amplitude, phase and speed will change regularly, rather than what we normally imagined. Therefore, we will use the microscopic variation law of the propagation of electric waves in the cable, and use the radar ranging principle to determine the distance of the cable fault point. Therefore, we must establish the concept of long line theory, impedance concept and reflection coefficient. Long line concept: A long line is a transmission line whose guiding line has a geometric length longer than or similar to the wavelength of the electromagnetic wave it transmits. It is generally considered that the line length L > λ/10 can be considered as a long line. For example, for a 1000 meter cable, the AC mains frequency is 50 Hz, its wavelength is 6000 km, and the 1000 m cable can be regarded as a short line. For a 5 MHz signal, the wavelength is 60 meters and the 1000 meter cable can be considered a long line. When the electric wave propagates on the long line, the current and voltage at each point along the long line are different under normal conditions, and the current and voltage at each point along the short line are the same. Long-line characteristic parameters: 1. Characteristic impedance Z0: The characteristic impedance of the cable is related to the cross-sectional area and size of the cable and the surrounding medium. The characteristic impedance of a coaxial cable is generally 40-100 ohms, and the power cable is generally 10-50 ohms. 2. Propagation speed: When Vp electric wave propagates in the cable, it will propagate forward at a certain speed, and the propagation speed is related to the dielectric material of the cable. For oil-impregnated paper cables, the propagation speed is 160M/us, and different cable media have different propagation speeds. 3. Reflection coefficient: The reflection coefficient is closely related to the load impedance. According to the analysis, the terminal reflection coefficient K2 is K2=(ZL-Z0)/(ZL+Z0) Where ZL is the load impedance. From the above formula we can draw the following conclusions: When the fault point is short-circuited, the fault point impedance ZL=0 K2=(ZL-Z0)/(ZL+Z0)=-1 Negative reflection occurs with an amplitude equal to the incident amplitude. When the fault point is open, the fault point impedance is infinite ZL=∠K2=(ZL-Z0)/(ZL+Z0)=1 Positive reflection occurs, and the amplitude is equal to the incident amplitude. When the impedance of the fault point is equal to or close to the characteristic impedance of the cable, ZL=Z0 K2=(ZL-Z0)/(ZL+Z0)=0 No reflection. When the fault point impedance is between 0-Z0, K2=(ZL-Z0)/(ZL+Z0)=-1~0 Negative reflection occurs with amplitude less than the incident amplitude. When the fault point impedance is between Z0 and âˆ, K2=(ZL-Z0)/(ZL+Z0)=0~1 Positive reflection occurs, the amplitude is greater than the incident amplitude. We talked about some physical phenomena that occur when power cables transmit high-frequency waves. These phenomena are impossible in our daily power transmission, but we use this physical phenomenon to test power cable faults. Let's take a look at the whole process of a pulse waveform propagating in a power cable. The pulse measurement method can intuitively observe from the cable fault tester that the cable fault point is open circuit or short circuit. The simplest test method for low resistance, short circuit and open circuit faults is pulse measurement. working principle: During the test, a low-voltage pulse emission waveform is injected on the fault phase, and the pulse propagates along the cable until the impedance mismatch occurs, such as an intermediate joint, a T-joint, a short-circuit point, an open-circuit point, or a terminal head, etc., at which point The reflection of the waves. We can see that when the fault phase is in a low impedance or short circuit state, the reflection coefficient is between -1 and 0, and the reflected waveform of the fault point is negative reflection. Reflections will also occur at the intermediate joint of the cable due to impedance mismatch, but the waveforms are relatively small, so we can determine the distance of the intermediate joint of the cable. If the load impedance ZL at the fault point is greater than the characteristic impedance Z0 of the cable, the cable will exhibit a positive reflection between 0 and 1. If ZL is much larger than Z0, the fault point will have no reflected waveform or the waveform is too small to be observed. When the pulse reaches the end point, a specular reflection will occur at the end of the cable. Therefore, the waveform we observe is the terminal waveform. The display distance is the full length of the cable. What happens when the signal is added to the good phase is the full length of the cable. The nature of the fault can be determined by the direction of the reflected waveform. When we add a positive polarity signal at the beginning of the cable, if the reflected waveform of the cable is a positive polarity waveform in the same direction, the cable fault is a high resistance fault and vice versa, or a cable short circuit. (Here is a point: the high-impedance or low-resistance fault reflected by the waveform is the ratio of the impedance of the fault point to the characteristic impedance of the cable, not the high-resistance or low-resistance measured by our daily megohmmeter. Let us call the fault point impedance greater than 500 ohms collectively referred to as high impedance.) The fault distance is calculated from the time difference between the measured pulse and the echo pulse. This involves the speed of the propagation of the wave in the cable we talked about earlier. The high-frequency wave propagates at a certain speed during the short-term transmission. Moreover, the propagation speed of the electric wave is related to the medium of the cable. For example, for oil-impregnated paper cables, the propagation speed is 160 M/US, and for cross-linked cables, the propagation speed is 172 M/US. During the T period, the high-frequency pulse propagates to the fault point by the cable end at the speed of VP. After reaching the fault point, it is reflected and returned at the speed of VP. The total travel distance is twice the distance from the beginning to the fault point. From the physics distance calculation formula S=V×T, the distance from the actual end to the fault point is S=V×T / 2, which can be directly read out through the display screen of the cable fault tester. Summarize the main points of the cable fault test principle: 1. The electric wave is carried out at a certain speed in the long-line propagation, and the amplitude of each point is different. 2. If there is impedance mismatch in the propagation of radio waves, reflection will occur. The reflection coefficient is between -1 and 0 when the resistance is low or short, and the reflection coefficient of high resistance or open circuit is between 0 and 1. 3. Different cables have different propagation speeds. 4. The obstacle distance is calculated from S=T×V/2. I talked about the principle of cable fault test and summarized four basic concepts. This is the basic idea of ​​testing cable faults. The following is an extension of the previous content. First discuss the nature and classification of cable faults: Cable faults can generally be classified into short-circuit faults, low-resistance faults, high-impedance faults, and open-circuit faults. The short-circuit fault is easier to understand, and the cable is completely short-circuited, and the cable fault point impedance is zero. Low-resistance faults are generally considered to be low-impedance faults below 100 ohms. Note: This classification is differentiated by the characteristic impedance of the cable. A high-impedance fault is when the fault point resistance is greater than 100 ohms. An open circuit fault is when the cable is completely disconnected. In the case of high-resistance faults, they can be classified into leaks and flashover faults. Leakage fault refers to the existence of a certain resistance at the fault point, between a few K and a few hundred megahertz. When the high pressure experiment is overexposed or the high voltage is not added at all. The flashover fault is that the resistance of the fault point is infinite, but when the voltage is raised to a certain value during the high voltage test, the leakage suddenly increases, the discharge is generated, the high voltage meter pointer swings, and when the voltage is lowered, the leak is leaked. Return to normal conditions. After understanding the condition of the cable failure, you can solve the problem with the right medicine. Cable faults with a fault point resistance of less than 1000 ohms can be measured using the simplest method (low voltage pulse test). The specific wiring is as follows: Connect the test end of the cable fault tester directly between the core wire of the cable and the sheath of the cable, and select the low voltage pulse test for measurement. Use the pulse generator inside the cable fault tester to generate a low-voltage pulse signal of about 100 volts to be applied to the cable. The signal will propagate along the cable on the cable. When the fault point is encountered (or the impedance is not matched), the signal vibrates. And to the two ends of the propagation, the cable fault tester will capture the transmitted pulse signal and the return signal from the fault point, and display it on the display screen by microcomputer processing, we can analyze according to the waveform. According to the theory we have mentioned before, the waveforms returned by the fault point will be different. The short-circuit fault and low-impedance fault waveforms will appear in a waveform that is opposite to the incident dial. The front pulse signal is the pulse signal from the cable fault tester, and the latter signal is the reflected signal from the cable fault point. We see that the transmitted pulse of this signal is opposite to the reflected pulse. We know from the theory of the reflection coefficient of the cable that the K value is negative, which indicates that the fault property of the cable is a short circuit fault. The nature of the cable fault is analyzed. The position of the fault point is analyzed below: the leading edge of the transmitted pulse is used as the starting point, the first cursor is fixed at the starting edge of the transmitted pulse, and then the second cursor is moved to the falling edge of the inverted waveform. The distance from the fault point is automatically calculated by the cable fault tester and displayed at the bottom of the screen. Looking at another signal pattern, we see that the transmitted pulse of this signal is in the same direction as the reflected pulse, and we know from the theory of the reflection coefficient of the cable that the K value is positive, which indicates that the fault property of the cable is high. Fault or open circuit failure. Similarly, using the leading edge of the transmitted pulse as the starting point, the first cursor is fixed at the beginning edge of the transmitted pulse, and the second cursor is moved to the rising edge of the same-directional waveform. We can see that at the bottom of the screen of the cable fault tester, The instrument automatically calculates the distance from the fault point. Using the low-voltage pulse test method, we can also easily measure the length of the cable. When the cable is fault-free or the impedance of the cable fault point is much larger than the characteristic impedance of the cable, the low-voltage pulse test waveform reflects the full length of the cable. The full length of the measuring cable is of great importance in cable testing. In order to meet the test of different cable lengths, we set two pulse width transmit pulses in the cable fault tester, where narrow pulse is used for cable fault test with cable length less than 1000 meters, and wide pulse is used for cable test greater than 1000 meters. . From the above application, we can see that the low-voltage pulse test method of the cable fault tester can easily measure the occurrence point of the cable fault, thus laying a good foundation for our next specific fixed point. Although the low-voltage pulse test method can solve the low-resistance or short-circuit condition of the cable fault, but the impedance of the cable fault point is greater than 1000 ohms, since the reflection waveform is small, the waveform is basically not seen, so the low-voltage pulse test is said. Applicable to low resistance conditions, high voltage flash test should be used for high resistance faults. The high voltage flash test method is introduced below. We discussed the method and scope of low-voltage pulse test. We know that the low-voltage pulse test method is only suitable for short-circuit, low-resistance and open-circuit faults. In reality, there are a lot of high-impedance faults and flashover faults, so it is necessary to adopt new Test methods to meet different cable fault tests. The high-voltage flash test cable fault is due to the use of a higher test voltage, cable faults are clicked to obtain the cable propagation data, so the high-voltage flash test can meet most cable fault tests. The high-voltage flash test can be divided into voltage sampling and current sampling. First, the voltage sampling is discussed. The wiring of the high-voltage flash voltage sampling is shown in Figure 2. (slightly) The high voltage flash test must first have a high voltage source, and our high voltage source is a negative DC high voltage generator. There must also be certain energy storage equipment. We use high voltage DC capacitors as energy storage equipment. In addition, there are high voltage discharge ball gaps, differential inductance, voltage dividing resistors R1, R2 and so on. Among them, R1 and R2 are sampling voltage dividing resistors, and the voltage waveform on the cable will be introduced into the test instrument after being divided by the voltage dividing resistor. Below we analyze the following working process: When we adjust the negative output voltage and charge the high voltage capacitor to a certain extent, the ball gap breaks down, and the high voltage is applied to the cable under test through the ball gap and inductance, because the ball gap is The negative high voltage is instantaneously broken down and applied to the cable, so we consider a negative high voltage pulse to be applied to the cable. According to the theory of long cable propagation, the negative high voltage pulse will propagate along the cable under test. When the negative high voltage pulse reaches the fault point, the fault point is broken down, forming an arc short circuit. At this time, the equivalent impedance will change, and the high resistance from the original unbreakdown will become a short circuit state. According to the principle of radio wave reflection, the short-circuit state K is -1, so a positive pulse will be generated at the fault point of the cable, and this forward pulse will propagate along the cable to the beginning, when the forward pulse reaches the beginning due to the presence of the inductance L (inductance) The pulse signal exhibits a high-impedance state with a reflection coefficient K of positive 1), and the forward pulse will be re-reflected into a forward pulse and propagate along the cable to the fault point, and when the pulse reaches the fault point again, due to The discharge process at the fault point is not over and is still in a short-circuit state. According to the principle of radio wave reflection, the short-circuit state K is -1, so the forward pulse will be re-reflected into a negative-direction pulse, which will again follow the cable to the beginning. Propagation, when the negative pulse reaches the beginning due to the presence of the inductance L (the inductance exhibits a high impedance state to the pulse signal, its reflection coefficient K is positive 1), the negative pulse will be re-reflected into a negative pulse and along the cable Spread to the point of failure. The above process is repeated in the cable until the energy on the storage capacitor is used up and the voltage is reduced until the fault point is discharged. The above is the mechanism of high-voltage pulse motion in the cable after the cable fault point is broken down by the high voltage voltage. At the same time, we should also pay attention to another phenomenon in the process of discharging the high-voltage cable at the fault point, which is the oscillation phenomenon after the breakdown of the high-voltage cable. We know that any cable exhibits a certain inductive reactance for high frequency signals, and it can be considered that this inductive reactance is a collection of each microinductor in the cable. When the breakdown point of the cable breaks down, an LC loop is formed. According to the characteristics of the LC oscillation loop, cosine oscillation will occur in the loop. We call it the cosine oscillation in the cable discharge. This oscillation will be judged by us. An important sign of whether the faulty cable is fully discharged. According to the mechanism mentioned above, in the high-voltage flash test of power cables, there are actually two phenomena in the discharge process of the high-voltage cable. In the measurement, the waveform we actually get is the superimposed waveform of the two phenomena. As shown in Figure 4 (omitted): On the graph showing the full waveform, we see the cosine oscillating waveform. On the local waveform diagram, we see the reflection waveform superimposed on the large cosine oscillation. The main basis for judging the cable fault point is the reflection waveform after the cable fault clicks. Whether the large cosine oscillation is generated is used to judge the cable. Whether the fault point is fully discharged, only the cable fault point is fully discharged, and the generated reflected waveform is the waveform we care about. The high-voltage discharge waveform obtained by the high-voltage flash test is shown in the figure. The lower figure is the large cosine waveform of the cosine generated after the cable is discharged. This proves that the cable has been broken down by the high voltage and fully discharged. What we are most concerned about is the reflected waveform superimposed on the cosine oscillation. We can see the expanded image of the acquired waveform in the main display area. Next, we analyze the image: according to the phenomenon that the high-voltage flash discharge pulse reflected back and forth in the faulty cable, the first rising pulse is the first breakdown of the reflected waveform for the cable fault, and then the falling pulse is the The pulse is pulsed twice to the reverse pulse that is reflected back after reaching the cable fault point. We analyze this pulse, move the first cursor of the instrument to the starting edge of the first pulse, move the second cursor to the falling edge of the reflected pulse, and the distance of the cable fault will be displayed at the fault distance of the instrument. Sometimes in order to verify its correctness, you can also test the second set of pulses for measurement. Move the first cursor of the instrument to the start edge of the second pulse, and move the second cursor to the falling edge of the reflected pulse. The fault distance of the instrument will be displayed. The distance from the cable failure. The two sets of data should be equal, so far we can determine the specific location of the cable fault point. Using this method can basically solve more than 95% of cable faults, so we should be proficient in this test method. Here are some special cases in the high voltage flash test: One. Fault near the terminal: When the fault point is near the terminal, there will be a breakpoint waveform that appears before the breakdown. Therefore, we will see a small negative reflection pulse before the rising pulse on our instrument. This negative pulse It is the reflected pulse of the cable terminal. The formation mechanism of this pulse is: when the high-pressure negative pulse generated by the ball gap discharge reaches the end point, and the fault point has not been broken yet, the cable end is in a high-resistance state, according to the reflection theory mentioned above, the high resistance The reflection coefficient is +1, so an in-phase pulse is generated and reflected toward the cable end, thus forming a negative pulse before the cable fault point is broken down. Therefore, we generally see that there is a fault wave front in the cable fault test. A negative wave exists and it can be judged that the fault point is not far from the terminal of the cable. two. The situation near the beginning of the fault point: When the fault point is near the beginning of the cable, the acquired waveform will have the following characteristics: 1 The acquisition waveform is quickly overshooted at the beginning. 2 A dense wavelet appears at the front because the first pulse has not yet been completed and the subsequent waveform is squeezed to form a continuous small amplitude pulse. 3 After a group of wavelets, it is basically a straight line, and there is generally no cosine shock. This is due to the fact that the inductive reactance is too small throughout the loop. When the waveform with the above characteristics is collected, it can be basically judged that the fault point is near the end. The distance can be calculated cumulatively using empirical formulas. Select 3-5 waves in the dense wavelet, look at the display distance, and then remove the distance with the number of selected waves to get the distance of the fault point. This kind of measurement has a small general error and is suitable for the judgment of the fault point where the fault distance is less than 50 meters. three. The case where the fault point does not discharge: When the discharge ball gap is adjusted too small or the capacitor energy is insufficient, the ball gap discharge may occur and the fault point does not discharge. If the fault point is not discharged, there will be no reflection waveform at the fault point, and the distance of the cable fault point cannot be measured. The waveform acquired is characterized by a gradually rising parabolic charging waveform, and some small negative pulses are superimposed on the rising curve. This negative pulse is the reflected waveform of the cable termination. The failure of the cable fault point can generally be divided into the following cases: the ball gap adjustment is too small, resulting in the ball gap being broken down in the case of low voltage, and this voltage is not enough to break through the fault point of the cable. The solution is usually solved by pulling the ball gap and increasing the working voltage. However, it should be noted that the voltage should be determined according to the insulation withstand voltage of the cable under test. Generally, the maximum voltage should be less than 2.5 times the withstand voltage of the cable under test. The capacity of the storage capacitor in the high-voltage flash test is of great significance for effectively breaking down the fault point of the cable. If the capacity of the storage capacitor is insufficient, the energy stored in the capacitor is insufficient to effectively break down the cable fault point, and the fault point will have no reflected waveform, and a non-discharge waveform will be formed. According to the test experience, for cables below 1000 meters, the capacity of the capacitor should be about 1.5 microfarads, and the minimum should not be less than 1 microfarad. For cables over 1000 meters, consider increasing by 1000 micrometers per 1 microfarad. And for low voltage cables of 380 volts. Due to voltage limitations, consider a 4-8 microfarad configuration per 1000 meters. four. Security issues: In the test of cable faults by high-voltage flashing method, due to the high test voltage level, special attention should be paid to the safety of the site during the test. The following problems should be noted in the test: 1. Grounding wiring problem: Since the current of this system is extremely high during discharge (about 20,000 volts of short-circuit current), the grounding wire of the system should be absolutely reliable. 2. Due to the large current of the discharge circuit, it is easy to cause the ground potential to rise in the state of poor contact, resulting in equipment damage or electric shock. Therefore, the ground wire of the discharge circuit should be grounded separately from the ground of the measurement circuit. 3. After all wiring is completed, it should be carefully reviewed and then energized. 4. When doing high-voltage flashover voltage sampling, do not connect the tester after the high-voltage system is connected, do the high-voltage air-belt test, and then connect the cable after further checking that the grounding system has no discharge phenomenon and the high-voltage system is normal. The fault tester performs high voltage sampling. 5. When using the ball gap in the high-pressure component box for fixed-point discharge, the output end should be directly connected to the discharge end of the ball gap, and the coil and the voltage dividing resistor should be disconnected. 6. For other safety issues related to high voltage operation, refer to the national safety standards for high voltage electrical experiments. The next discussion is another new test method called high voltage flash current sampling. The process of sampling the high-voltage flash pulse current is to record the transmission process of the transient electromagnetic wave of the fault click and discharge in the cable fault test by using the current sensor. The distance of the cable fault is calculated according to the time at which the discharge point of the fault point is reflected back and forth between the test end and the fault point. The required equipment is configured as a high voltage voltage generator (commonly known as high voltage PT). The general cable fault test configuration is about 3KV, control protector, high voltage pulse capacitor, discharge ball gap, current sampler DL and so on. The function of the current sensor is to transmit the instantaneous current change signal in the capacitor C discharge circuit during the test to the cable fault tester through the electromagnetic coupling of the space. During the test, when the regulation voltage is high to a certain extent, the discharge ball gap is broken, and the electric energy in the high-voltage storage capacitor is transferred to the cable through the discharge ball gap to form a discharge pulse current, and when the voltage on the cable reaches the cable failure point When the breakdown voltage is applied, the cable fault point generates a discharge. A discharge pulse is formed on the current sensor. According to the characteristics of the fault point introduced in the previous section, if the surge voltage-Ee amplitude is greater than the breakdown voltage of the discharge gap of the fault point g, the discharge gap will be ionized when the surge voltage is transmitted to the fault point along the core line. A short-circuit discharge is formed, and a large kick current is generated in the loop, and the kick current is received by the current sensor to form a trigger pulse. At the same time, a positive jump voltage of -Ec→0 is generated to be incident on the test end of the cable and the terminal end of the cable (the process of incident transmission to the terminal may be disregarded). When the positive jump incident wave is transmitted to the test end, it is considered that the ball gap is still ionized and short-circuited at this time, and the storage capacitor C can also be considered as a short-circuit state to the positive step voltage. It can be known from the cable characteristics and the reflection coefficient concept that the test end The external impedance becomes very low due to the storage capacitor C, which is much lower than the characteristic impedance of the cable, and the signal incident from the fault point is short-circuited, that is, the reflection coefficient is close to -1. Therefore, a negative reflection will be produced at the test end. The reflection will move toward the cable fault point. When the cable fault point is reached, the fault point is broken down by the incident pulse and then propagated to both ends, so that multiple reflections consume energy until the energy is consumed and the discharge process ends. |
Brandt Vsm 300 Scalping Shaker Screen
Replacement Scalping Screens for Top Deck of Brandt Vsm 300 Shaker
SJ-Brandt VSM 300 Scalping shaker screen is manufactured as the replacement screen for Brandt Vsm 300 Shale Shaker. It is installed on the top deck of the VSM 300, which are used to scalp off large volumes of solids. Thus protecting the finer mesh , The scalping screen is usually sized from API 10 to API 325, ShengJia promises you high quality VSM 300 screen at reasonable price. And there are steel frame and composite screens optional.
Technical Parameter
- Mesh Material: stainless steel 304/316/316 L.
- Body Material: Q235 steel/composite.
- Screen Type: pretension, repairable.
- Screen Layered: single, dual or triple layered.
- API RP 13C Designation: API 10 – API 325.
- Color: green, black.
- Package: 2 pcs per carton, packed in wooden case
Adaptable Shale Shaker Model
SJ-Brandt VSM 300 Scalping shaker screens are used as the substitute screen for
- Top deck screen (3 screens) of Brandt VSM 300 shale shaker.
- Brandt VSM 300 vibrating screens.
- Brandt VSM 300 mud cleaner.
Competitive Advantage
- Composite frame sieve, anti-rust.
- Top-quality stainless steel wire mesh for longevity.
- Steel framework & composite framework optional.
- Manufactured according to the API RP 13C (ISO 13501).
- Scientific & reasonable cost control system for competitive price.
- Adequate inventory in the shortest time to meet customers' demand.
Remarks:
Brandt, VSM 300, Scalping are marks of Varco I/P, Inc.
ShengJia only produces the replacement screens but not original from Brandt.
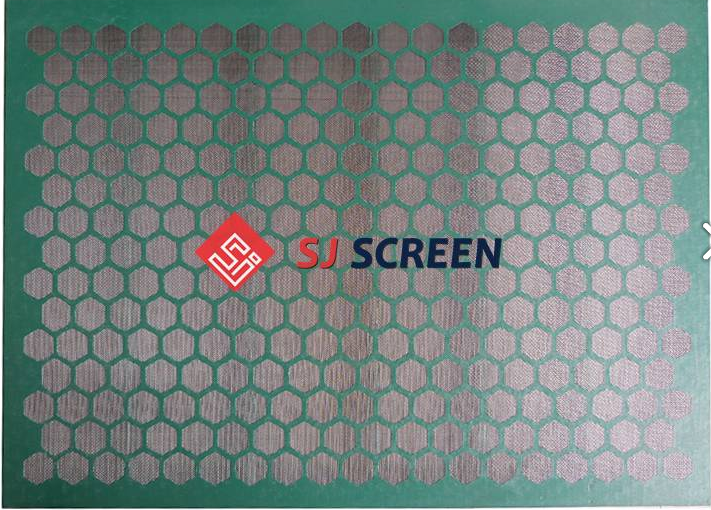
Brandt Vsm300 Scalping Shaker Screen
Brandt Vsm300 Scalping Shaker Screen,Vsm 300,Screen Mesh Sizes,Deck Screens
Anping Shengjia Hardware Mesh Co.,ltd , http://www.oilshakerscreen.com