Abstract From "Intelligent Manufacturing: Subversion and Reconstruction of Future Industrial Models and Formats", [German] Alto Brockman's product without a corresponding process is itself equivalent to garbage. Products that were defined as production results in the past are now the product of the production process...
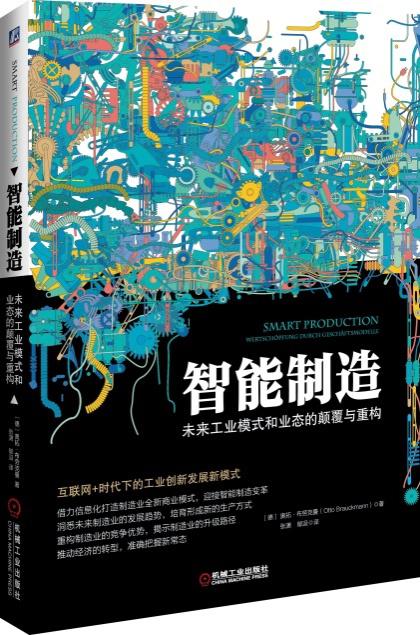
From "Intelligent Manufacturing: Subversion and Reconstruction of Future Industrial Models and Formats", [German] Alto Brockman
A product without a corresponding process is itself equivalent to garbage. Products that were defined as production results in the past are now the product of the production process. Therefore, the market power and economy of the products are based on processes. But the logic of the production process is different: the process can be calculated relative to traditional production parameters, and the economics it represents is not based on process time, but on the connection point of the process. A perfect intersection between multiple processes without any errors does not exist. Every possible error can happen at some point. As long as there is a mistake in the entire cooperation, it will affect the entire process. The reliability of the entire process chain is related to the number of joints and the safety (distribution, repeatability, and planability) of each point. The management of connection points has led to new thinking, as defined in the ISO 9001 ff/TS 16949 standard: “The use of a series of processes in an organization, coupled with the identification and management of the interaction of these processes, can be considered as A process-oriented approach. One of the advantages of the (ISO 9001 ff) process-oriented approach is the ability to continuously regulate the linkages between individual processes (ISO 9001:2000).
One-piece and overall revenue
The sequential logic of the process is certainly not the same as the sequential logic of the production process. The production process simply accumulates the time required for each production step. We use a simple crap game to illustrate this difference.
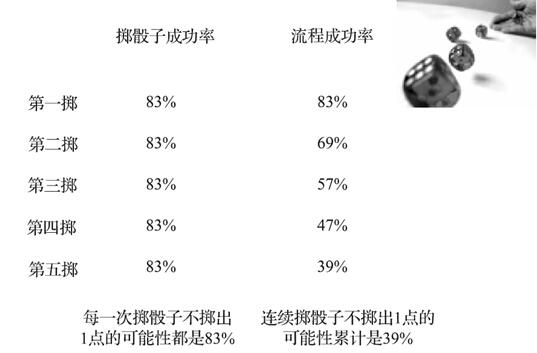
Figure 1 Rolling the dice and the success rate of the process
We throw 5 dice in front and back, and define 2 to 6 as innocent products, and only 1 is defined as defective. This way we will have an average of 5/6 chances of success every time we roll a dice, which is 83%. The average success probability of 5 dice is also 83%. If we look at the possibility of a continuous success of five dice, that is, five consecutive throws, the probability of continuous success is only 39%. This means that the probability of an error is 61%. The possibility of an error every time a dice is thrown will be added.
Putting the above case in production means that even if we have a machine with a successful productivity of 83% (this success ratio is not bad, the real metal processing industry is much lower than this value), in a row After 5 production steps, only 39% of the possibilities will result in a successful product, and 61% will have a defective product and need to be reworked. This extremely simple case tells us that even with only five production steps, that is, only four steps, the success rate of the process will drop drastically, hiding the huge potential for improvement.
So the efficiency of production depends on the complexity of the process chain, the number of junctions, and the different types of individual processes. Different types represent a decentralized process result that reduces the accuracy of process repeatability and potentially makes the process more difficult to plan. The resources consumed by inefficient processes, such as unplanned waits and berths, are much higher than the resources consumed by low productivity. Because for the latter, the potential has almost been developed, and almost all companies have modern production techniques. In comparison, the potential for improvement in the process is enormous. The economics of a company depends on the intersection of processes.
Therefore, the ISO 9001 standard defines production efficiency based on the cooperation between processes. “If companies want to operate efficiently, they need to identify, control and guide a large number of activities that are related to each other.†(ISO 9001 ff) Although many companies have signed this agreement, they are very controlled according to standard processes. Few people are really doing it.
Again, this reference to the ISO 9001 ff standard: “One of the advantages of a process-oriented approach is the ability to continuously regulate the links between individual processes.†(ISO 9001:2000)
Case model - assembly machine
Figure 2 shows a case of an assembly machine process, which can also be placed in other processes. There are eight prerequisites for the assembly process, such as machine preparation, employee readiness, material availability, and tool availability. The success of the assembly process depends on the success of each individual step. Each individual step and condition brings the risk of error: the machine is not ready, the tool is not ready, the material is not ready, and so on.
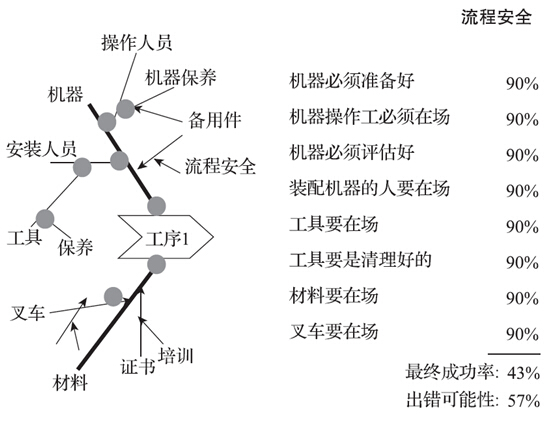
In Figure 2, we assume eight preconditions for the process, each with an average success rate of 90%. Even if there are only 8 prerequisites, and the success rate of each condition is quite high, the overall success rate of the final process is only 43%, 57% will be problematic. Or another way of expression: 57 of the 100 assembly machines need to be interrupted, and only 43 can be completed as planned. This 43% ratio is called the process success rate, or if it is a process chain, it is called FPY (First Pass Yield).
This total success rate obtained by multiplying the success rate of each step is also widely used in reality. The reason for this success rate is the ubiquitous delay: either the machine is configured to be ill, or the material is not yet ready, or the tool is not ready. Failure steps represent a decline in efficiency, while corporate resources are still being used. The failure step is accompanied by a large number of follow-up costs, such as overproduction (morning time) or underproduction (waiting time).
Production efficiency and variance
Process fragmentation (such as availability) plays a crucial role in the economics of the business, and Figure 84 shows the reality-based production relationship (Rehbehn and Yurdakul, 2003). Figure 84 shows the relationship between the degree of process dispersion (scattering index Sigma) and the cost of error analyzed by Siemens.
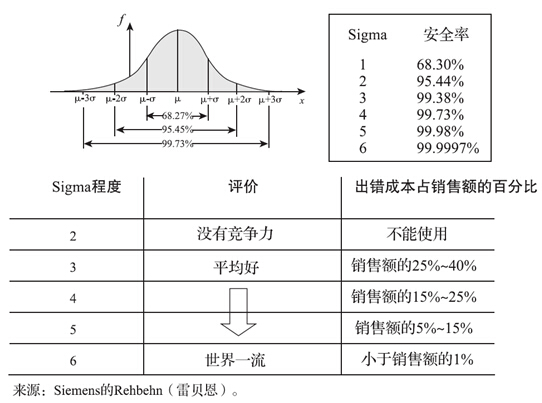
Real-life business processes generally face hundreds of different prerequisites. The authors believe that the process safety level is 2σ (the success rate of each step of the process reaches 95.44%) is not competitive. The last column in Figure 3 shows the relationship between the safety level σ of the process and the production cost. The smaller the dispersion of the process at the junction, the smaller the loss caused by the error.
Sigma (σ) is used to indicate process dispersion, and σ level can be regarded as an important indicator of production economy. The data in Figure 84 is based on real production conditions. The data shows that even if the process has a very high success rate of 99.38%, there are still 25% to 40% of sales to be used to pay for errors in the process. From these data, it can be seen that the improvement of the σ level has a very obvious effect on the economic improvement. The cost of failure listed here is unbelievably high compared to the average after-tax rate of return for 3.5% of machinery and electronics companies.
Conclusion: From a process perspective, productivity is based on variance and process connection points. The impact of the variance in the process on the economy is higher than the impact of technology and production on the economy at a multiple of 20. “If you want to increase the efficiency of your business, that is, increase productivity and reduce costs, then achieving a 6σ level will be the best choice.†(Walch, 2005)
Hidden factory
For the employees of the company, especially the workers on the production line, the company's value stream and cost calculations are not directly recognizable. A record and calculation that is closely related to the process and updated in real time is not used in practice. What is more widely used in practice is just the record after the operation, and only the parameters that can be counted or measured are recorded. There is no clear understanding of how much resources are actually consumed. Unit costs are difficult to count, and there are always reasonable excuses for the time resources wasted by waiting and parking. For example, when a worker needs to interrupt the process of assembling a machine, his subconscious does not feel that this will affect productivity, because he feels that the machine will "immediately" receive the next task to continue operation, and will not affect To efficiency and even economy. It should also be noted that the increase in inventory during the production cycle will in turn make employees more calm. Because if a lot of boxes are filled with goods, there will be a hint that the company is operating well, and it will make the job more stable. But in fact all unplanned production interruptions can lead to invisible waste, as shown in the next case.
For programs that are not recognized in the enterprise, Boston University School of Management professors Miller and Foreman are named "hidden factories." Because these indirect parts actually hide a lot of productivity (Müller, 1992).
Parking is more expensive than production
Figure 2 shows the flow of an assembly machine with eight preconditions for the entire assembly process. The efficiency parameter of the process chain is FPY, which is the proportion of the process's success (Rehbehn and Yurdakul, 2003). Figure 4 re-seals the content of Figure 2. When each step of the eight process steps has a 90% success rate, the final total success rate is 43%. In other words, there are 57 out of every 100 planned assembly processes that need to be interrupted for various reasons and cannot continue. Interruptions specifically represent waiting materials, waiting for tools, waiting for workers, and so on. This also means that the tool has to be removed and put back into the warehouse. Other resources are the same, such as materials and other accessories (measurement tools, test reports, etc.). Next, you need to arrange new tasks and check the feasibility, because the FPY risk also exists. In some cases, disruptions can also incur additional costs, such as an emergency, special shifts, or overtime, or even a helicopter that goes straight to Wolfsburg. So waiting or parking due to interruptions is more expensive than production.
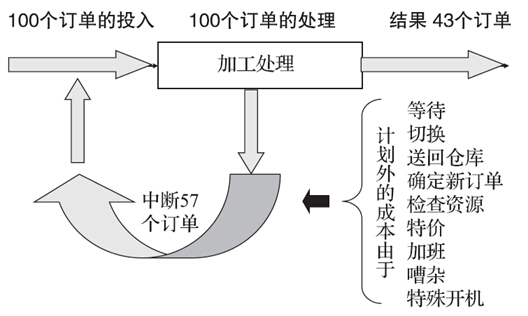
Therefore, the assumption that the above-mentioned machine usage rate has nothing to do with the waiting and berthing time of the material is simply wrong.
Loss calculation
The production process forms a complete set of events in sequence. At each process handover point, there are risks that affect process accuracy (distribution), such as too much, too little, too early, too late, wrong place, wrong quality, etc. Taguchi (Takaguchi) has developed a method for calculating losses in relation to the relationship between the faced differences and the expected values ​​and the resulting losses. This method can calculate the loss represented by the difference, even if it is within the margin of error. Although Taguchi began to develop this method with a deliberate reference to a more reliable design, and mainly used in the field of technical processing, his method can also be well transferred to other processes. Taguchi mainly emphasizes the dispersion of individual target variables: for the customer, the usability of the product continues to decrease as the error increases.
The margin of error in a process cannot be considered as a production error threshold, but as a loss to calculate. According to the following statement: the loss caused by the error of each process target is squared according to the magnitude of the error. The process objectives may be time (product completion), location (transportation target), quantity (overproduction or underproduction) or quality (extra detection, reprocessing, destruction).
Every worker in practice knows: "There is always an accident." It is not the lack of materials, the machine is not ready, the workers are sick, or the tools are not. Typical daily effects include unplanned production interruptions, failure to produce as planned, and waiting or berthing time, mold preparation cannot be completed. Based on these issues, one goal of process operations is to take steps to minimize the root causes of these errors.
In addition to the increased safety of the junction, the number of junctions (ie complexity) is also critical to the calculation of losses. If in the case of the dice in Figure 1, there are not 5 dice but 10 dice, or 10 production steps but 10 according to the production process, then the final success rate is only 16 %, and in fact, the 10 steps are not too much for real-life business operations. The number of steps also represents the number of errors that can occur (Opportunity for Defects). This case shows that the process cannot be judged after the end of the process, because it is too late, but needs to be adjusted in the process (with the production process) (Rehbehn and Yurdakuhl, 2003, p. 52).
1.Our Polycarbonate Sheet,tiles will not be broken within 10 years under the weather and impact strength. Yellowing index and transmittance loss will not exceed the value defined by warranty;
2.We guarantee for the surface of pc sheet not caused collateral damage due to hail impact, but our guarantee not including the damage caused by other impacts such as scratches, abrasions, exposure, self-storage, transportation, handling and improper installation, physical and chemical changes occur.
Solid Polycarbonate Sheet Greenhouse,Solid Polycarbonate Sheet in Philippines,Solid Polycarbonate Sheet Price Philippines,Solid Pc Embossed Sun Sheets
FOSHAN KASO BUILDING MATERIAL CO.,LTD , https://www.kasocover.com