Materials are the material basis of aviation weapons and equipment. Advances in materials technology continue to drive the performance and upgrading of aviation weaponry. Significant progress has been made in advanced composite materials, high-performance metal structural materials, special functional materials, and electronic information materials, and the development of high-temperature, intelligent, micro-nano and designable.
I. The direction of composite materials New technology for mass production of carbon fiber In January 2016, a research team consisting of Toray, Teijin, Mitsubishi Riyang and the University of Tokyo developed a propylene fiber material that is not easily melted in a high temperature environment. There is no need to carry out the preparation process for preventing melting, and the electromagnetic wave is used to directly heat the fiber to replace the conventional autoclave heating process, so that the carbon fiber production speed is increased by 10 times. In addition, the new process can halve energy consumption and carbon dioxide emissions during production.
Ceramic Composites Innovation In August 2016, NASA said that with the support of the revolutionary aviation concept project, researchers are studying ceramic-based composites (CMC) and protective coatings to replace current aerospace engines. Nickel-based superalloy for medium application. In addition, Japan's Ishikawajima Heavy Industries (IHI), Ube Industries Co., Ltd., and Shield Co., Ltd. will also trial and manufacture CMC aircraft engine high-pressure turbine blades in 2017.
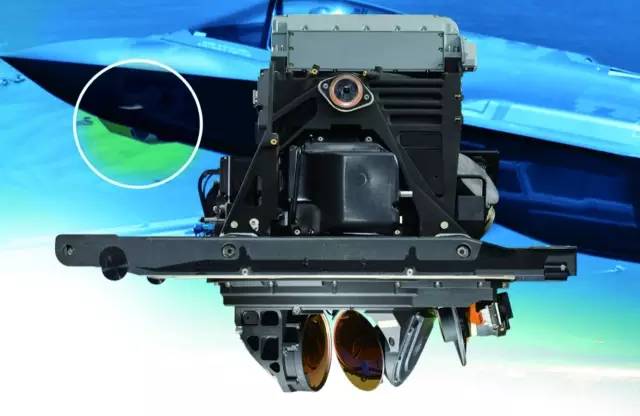
Platform housing for F-35 photovoltaic systems made with new alloys
Second, the direction of metal materials Light alloy materials In May 2016, the American Institute of Lightweight Materials Manufacturing Innovation launched the titanium alloy and aluminum-lithium alloy project, aiming to better predict the performance of engine materials by improving the calculation model.
é“Aluminum alloyé“Aluminum alloy is a two-phase metal. The melting point and solid phase temperature of the two phases differ by 627 °C, which is difficult to cast and process. It has been only powder processing, the component is expensive, and the manufacturing time-consuming scrap rate is high, which limits the application of the alloy. . In 2016, Lockheed Martin (Loma) cooperated with companies such as IBC Advanced Alloy to develop a new aluminum-bismuth alloy Beralcast, which replaced the traditional powder metallurgy with a special casting process to realize the inertial platform shell of the F-35 photoelectric aiming system. Near net shape, it is expected to save 30% to 40% of manufacturing costs and significantly shorten the manufacturing cycle.
New Cast Iron Materials In January 2016, Engineering Propulsion Systems (EPS) designed a compact, lightweight, rugged aerospace diesel engine using the more compact "Compact Graphite Cast Iron" (CGI). This compact graphite cast iron achieves strength and crack resistance by adding tight graphite particles to interlock the iron matrix. Compared with ordinary gray iron and aluminum alloy, the tensile strength is increased by more than 75%, the hardness is increased by 45%, and the fatigue strength is nearly doubled. This material is currently used in the engine crankcase of EPS.
Third, the direction of special materials Broadband adjustable radar absorbing super material In February 2016, the United States Idaho State University used liquid gallium indium tin alloy instead of solid metal to manufacture the super-material internal structural unit - open resonant ring, developed a new type Flexible stealth metamaterial. The material can be continuously adjusted in the absorbing band of 8G to 11GHz, and the RCS is attenuated by 40 to 60dB. Compared with the radar absorbing material of the active equipment, the stealth performance is improved by 100 times. This achievement opens up a new technical approach for the study of broadband adjustable absorbing materials.
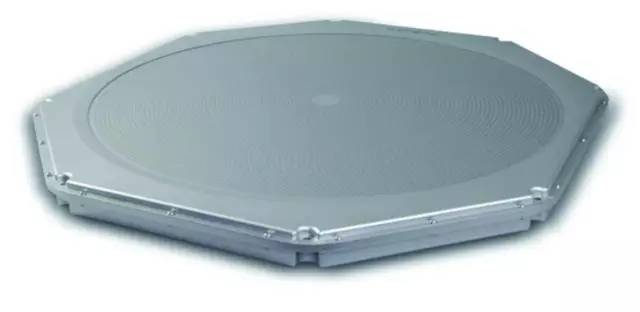
Kymeta's metamaterial antenna.
High-temperature resistant ceramic materials In August 2016, Russian researchers developed a multilayer ceramic structural material based on a mixture of ceramics of silicon carbide and zirconium diboride, which is expected to withstand the extreme temperature of 3000 ° C and can be used for lifting. The temperature of the jet engine's combustion chamber can also be used to insulate the spacecraft as it re-enters the atmosphere or to create a sensor shield that measures the temperature of the engine. In December, the Imperial University of England team found that compounds of tantalum carbide and tantalum carbide (80% 钽 and 20% 铪) have a melting point of 3,905 ° C, paving the way for future applications in extremely hot environments, such as next-generation supersonics. The thermal shield of the aircraft and the fuel cladding of the nuclear reactor.
Self-cleaning, anti-reflective, anti-microbial coatings In September 2016, the University of Basque Country in Spain, in conjunction with the IBM El Marden Research Center in San Jose, USA, developed a coating that is resistant to microbial adhesion, self-cleaning and anti-reflection. The coating exhibits phase separation properties that significantly reduce microbial adhesion. The self-cleaning function is achieved by spraying inorganic silicon nanoparticles with hydrophobic properties on the acrylic coating to form a superhydrophobic surface with good strength and toughness. The anti-reflective property is achieved by introducing a porous structure, so that the effective reflectance of the coating is lower than that of the substrate; at the same time, in order to reduce the influence of the pore structure on the mechanical properties of the coating, the researchers have determined the optimum range of porosity.
Carbon Heatsink Materials In August 2016, United Technologies Aviation Systems (UTAS) supplied new tires and brakes to the US Air Force's 475 F-15 fighter jets. The new carbon brakes feature a patented carbon heat sink material that is four times longer than current brake systems; the new tires feature a boltless lock ring design that significantly reduces repair time and costs, reduces part count, and enhances the F-15 fighter aircraft. Team performance and performance.
Fourth, the direction of electronic materials Hypermaterial antenna In March 2016, Kymeta said that its mTenna metamaterial antenna has entered the military market. The mTenna antenna is automatically calibrated to adjust the reception of electromagnetic waves during flight. The manufacturing process is similar to that of a liquid crystal display or a smart phone glass screen. The cost is only 15,000 to 25,000 US dollars, which is significantly lower than the phased array antenna and the electric sweep antenna. In addition, the antenna consumes only 10W of power, transmits and receives, and weighs about 18kg, which can be carried by a single person.
Two-Dimensional Gallium Nitride Semiconductor Materials In August 2016, materials scientists at Pennsylvania State University used a graphene encapsulation method to add gallium atoms between two layers of graphene using a migration enhanced package growth (MEEG) technique. A chemical reaction is initiated to form an ultra-thin layer of gallium nitride encapsulated in graphene, and a two-dimensional gallium nitride material is first synthesized. This material has excellent electronic properties and strength and will have a transformative impact on the electronics industry.
Gallium Liquid Metal Alloy In May 2016, the US Air Force disclosed its ongoing radio frequency electronics research project for gallium liquid metal alloy (GaLMA). GaLMA consists of liquid metal, gallium and other conductive metals. It is light in weight and variable in configuration. It is important for platforms that strictly limit size, weight and power. It can extend flight time, increase load capacity and reduce aircraft traditional RF. Aerodynamic drag caused by the structure. GaLMA-based liquid electrons are a completely new approach and a completely different form of material for traditional RF electronics, allowing antennas and electrical contacts to be physically movable and reconfigurable so that the shape and function of the electronic components can The task needs to change.
Transparent ferromagnetic materials On October 9, Japanese researchers developed a transparent ferromagnetic nanoparticle film material, which is made of a mixture of nano-scale magnetic metal particles of iron-cobalt alloy and aluminum fluoride, which is expected to be used for windshield in aircraft. A new generation of transparent magnetic devices that directly display information such as oil volume and maps on glass, bringing innovative technological developments to industries including electrical, magnetic and optical devices.
Aviation Materials: Opening the Golden Age of the Decade 1. Summary
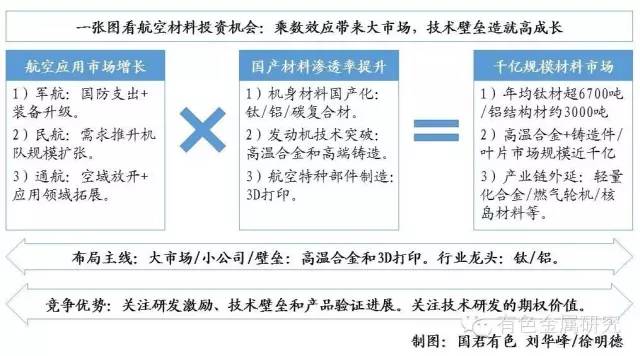
The material industry chain is complete, and the market for import substitution and maintenance is huge. Assume that by 2030, the demand for Chinese civil aviation/military aircraft is about 2,800 units / 2,200 units, and the fleet size is about 5,500 / 6,000 units, which corresponds to about 98,000 tons of titanium alloy demand, and 250,000 pieces for high-end casting and 3D printing parts. Civil aviation engine maintenance inspection demand is about 12,000 units, and military aviation engine demand is more than 5,000 units. With the domestic aviation materials gradually entering the supply system of China Commercial Aircraft and AVIC, from the perspective of material independent supply guarantee and airline operating cost control, the realization of domestic replacement of aviation materials in the future will become the trend of the times, and the localization of aviation materials has been gradually advanced. The import substitution and maintenance market has a broad space.
Titanium, new alloys, superalloys and 3D printing are the first to benefit. We judge that in the 2016~2017 big aircraft first flight and military aircraft replacement window period, listed companies that have already entered the domestic military aircraft/large aircraft supply chain certification are expected to achieve a reversal of performance and open up the growth space. Among them, titanium materials with advantages in production capacity and casting process, aerospace parts manufacturing relying on 3D printing technology to achieve traditional casting replacement, and aviation engine blade and engine maintenance are expected to take the lead.
2. The aviation industry is expected to usher in a golden age 2.1. The civil aviation manufacturing industry is gradually gaining harvest. The international aviation industry is rapidly increasing its demand for aircraft. In 2013, the new orders for Boeing and Airbus's civil aircraft reached a historical peak, indicating that the demand for aviation materials will remain high in the next few years. As we can see from the aircraft orders, there is a growing trend in the volume of orders for the aviation industry. In addition, the order fluctuation period is about 10 years. From a global perspective, the aviation industry's demand for civil aircraft is expected to attract a new round. cycle.
The demand for Chinese passenger airliners is strong. According to Boeing's forecast, in 2013-2032, the number of new civil aviation aircraft required in the world was 35,200, of which 5,580 were in China, accounting for 16%, and the Chinese market was worth 780 billion. Among them, 3,900 single-aisle aircraft, accounting for 70%, the huge market provides a broad space for the development of trunk and regional aircraft independently developed by C919 and ARJ21.
The ARJ21 stocking period is coming soon, and the C919's first flight is getting closer. On November 29, 2015, China's first medium and short-range new turbofan regional aircraft ARJ21, which was developed in accordance with international standards and has independent intellectual property rights, will be delivered to Chengdu Airlines and enter the market. From the first flight of ARJ21 to the operation of the flight route, the aircraft passed the airworthiness review of China Civil Aviation, the FAA shadow review, and the follow-up approval review, indicating that the aircraft indicated that the project level meets the world's most stringent aviation safety standards. The design and assembly technology of the regional jet passenger aircraft can be maturely used in airline operations, and the door of the domestic passenger aircraft civil aviation market has been opened. The prospects for the development and marketization of domestic jet passenger aircraft are expected.
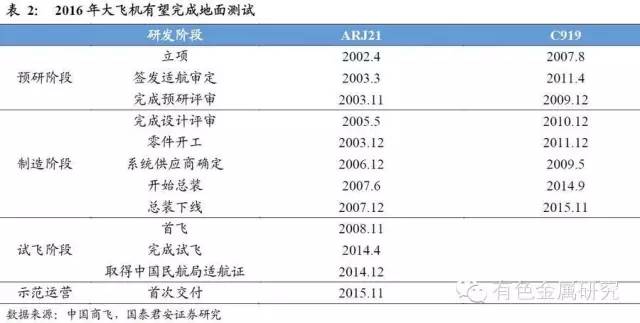
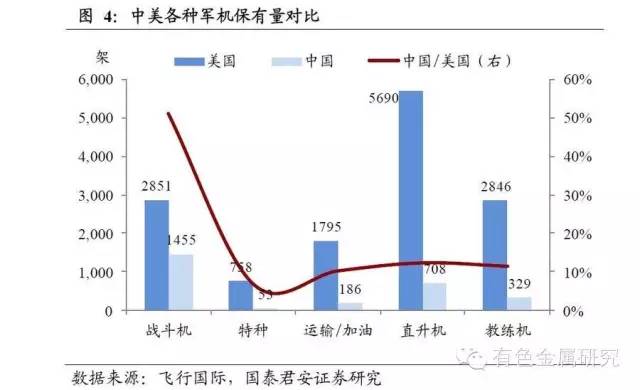
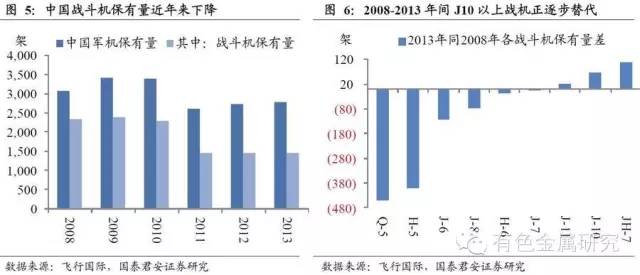
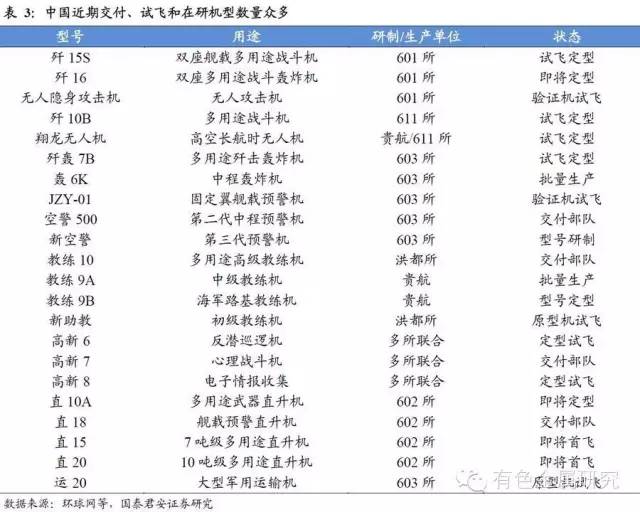
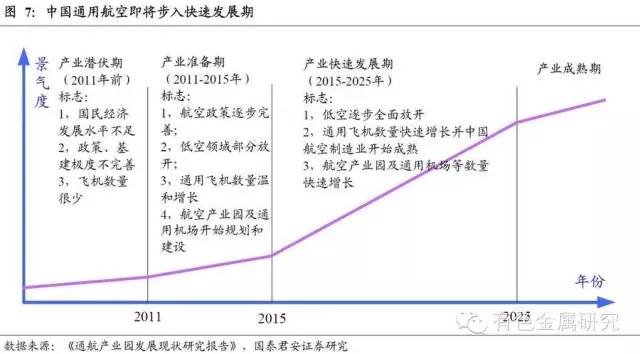
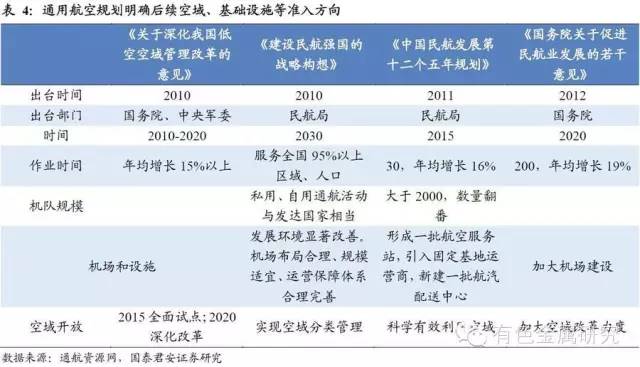
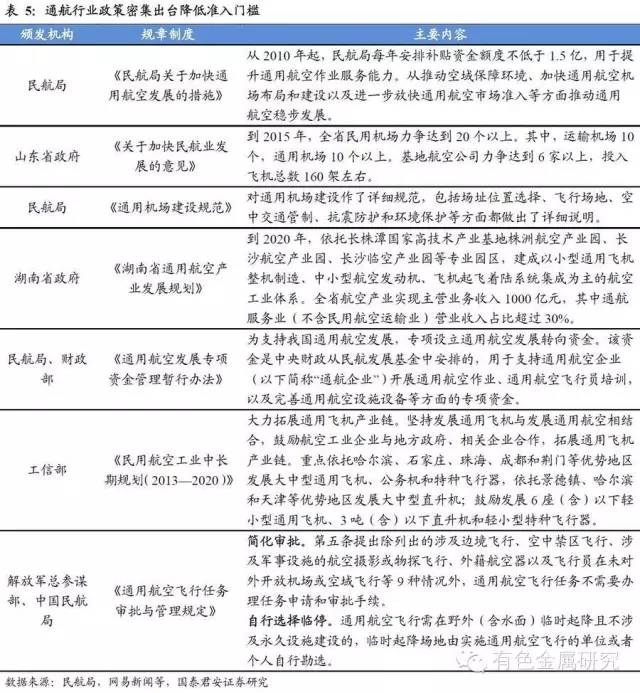
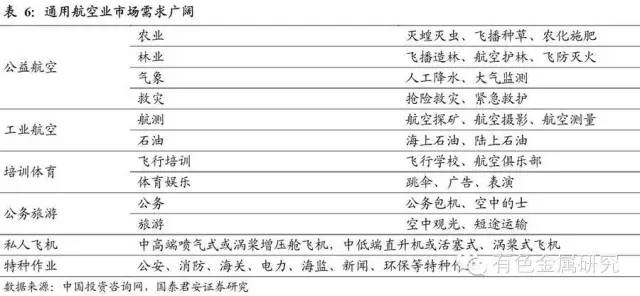
3. Material Perspective: Localization and Maintenance Demands Stimulate the Aviation Material Market 3.1. The first generation of aircraft, the material of the belt has become the core of aircraft development and manufacturing. Due to the increasing economic requirements of civil aviation for aircraft, various types of multi-purpose navigation aircraft and drone applications are emerging, and structural weight reduction and fuel efficiency improvement have prompted the large-scale application of various new types of aircraft in aircraft. The demand for new materials for the improvement of the performance of aviation military aircraft is also gradually reflected. Every time the aircraft is replaced, it is accompanied by innovations and applications of body materials, structural materials, engine materials and various component materials.
3.2. Titanium: In the domestic military aircraft and passenger aircraft components, the penetration of large titanium materials in China's aerospace industry will continue to rise. Titanium and its alloys are increasingly used in the aerospace industry due to their excellent properties in terms of specific strength, fracture toughness, heat resistance, corrosion resistance and the like. At present, the world aerospace titanium market is mainly concentrated in the United States, Russia, Europe and other countries and regions. From the perspective of improving the performance of aircraft, in the future, the amount of titanium used in large-scale passenger aircraft and advanced fighters in China will continue to climb. The amount of titanium alloy used in commercial feeders ARJ21 in China is 4.8%, and the amount of titanium alloy used in commercial trunk passenger aircraft C919 is as high as 9.3%, slightly higher than Boeing 777 (Boeing 777 is 7%-8%). As the country's support for the aerospace industry has increased year by year, the demand for downstream high-end titanium materials may lead to an explosive period as China's civil and military aviation fields may usher in explosive development opportunities.
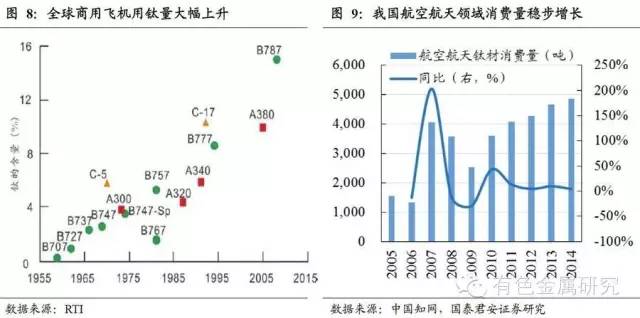
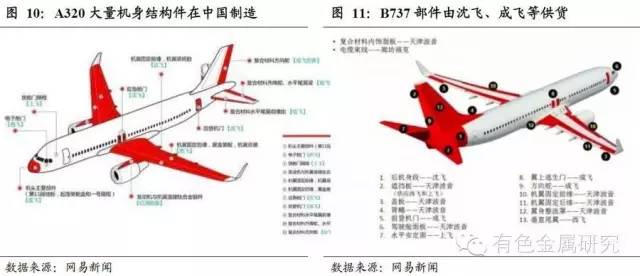
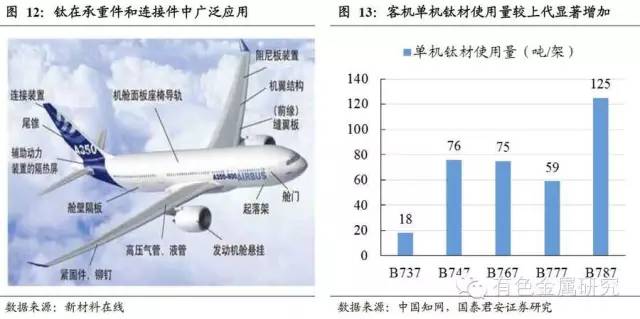
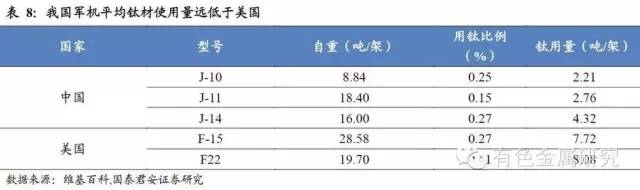
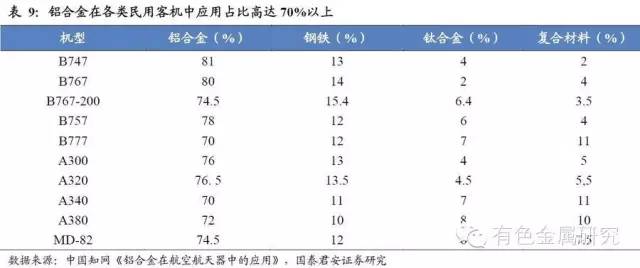
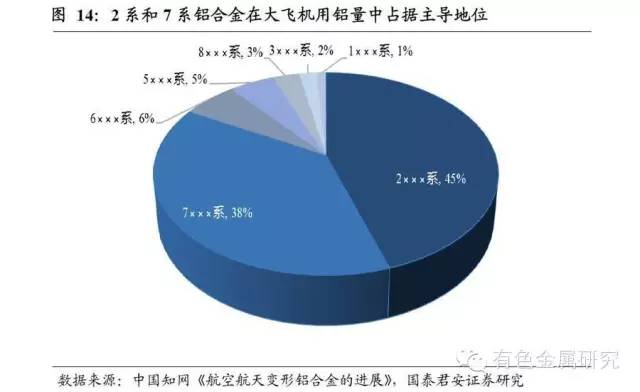
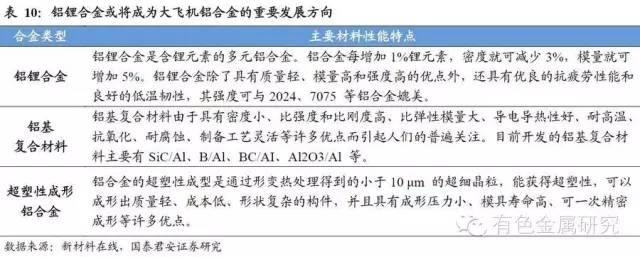
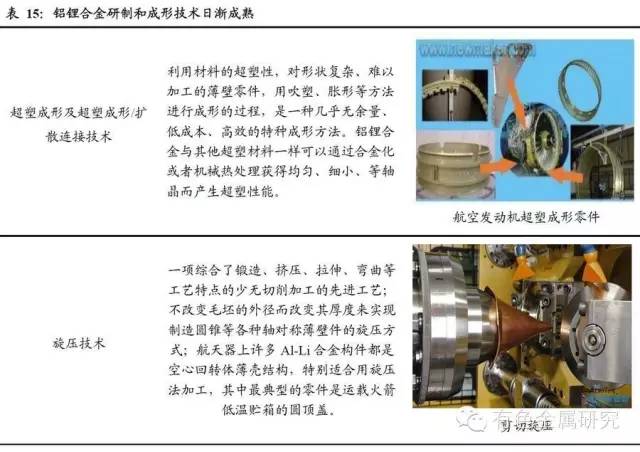
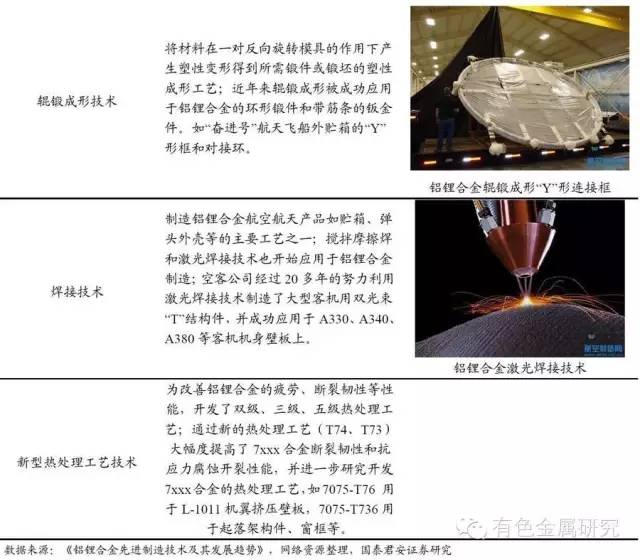
3.4. Engine materials: Focus on high-temperature alloys and single-crystal blades 3.4.1. Superalloys The global market for high-temperature alloys is huge, with aerospace sector accounting for up to 55%. As of the end of 2012, the annual consumption of global superalloys has reached 280,000 tons, and the market space has exceeded 10 billion US dollars; especially in the aerospace industry, the consumption ratio is more than 55%. We believe that the downstream aerospace industry continues to increase. Driven by the demand, the demand will continue to increase with the development of high-end industrial in the world.
Superalloys are the core material of the engine. Engine core materials include titanium alloy blades for fans and compressor front stages, superalloys for afterburners and low pressure turbines, single crystal discs and blades for high pressure turbines, and superalloys for nozzles and combustion chambers. In general, iron-based high-temperature blades are used in combustion chambers, after-stage compressors, etc., which have high operating temperatures and require high pressure.
The annual demand for domestic aero-engines to pull high-temperature alloys is about 1,200 tons. Considering that the domestic aviation engine is mainly used in the military field, it is assumed that the demand for aero-engines will be about 3,200 units in the next 10 years, each weighing about 2 tons, the superalloys account for 50% of the total mass, and the finished product rate is about 50%, taking into account factors such as spare parts. The demand for high temperature alloys for aerospace engines exceeds 12,000 tons.
3.4.2. Blade forging and processing of single-crystal blades for aero-engines will shrink with foreign generations, and the market space is huge. Turbine blades are one of the core components of aerospace engines, and temperature tolerance is also a key factor in improving engine efficiency. The final stage compressor and the first stage fan directly contact the high temperature airflow above 1500 degrees Celsius, and at the same time bear huge pressure, and the material requirements are high. The single crystal blades that Chengdu Aerospace intends to put into production are expected to be successfully developed for aviation turbojet engines and eliminate the generation difference between domestic engines and imported products. Considering the requirements for the inspection of four generations of aircraft, large unmanned aircraft and third-generation aircraft, it is assumed that 1000 fighters will be installed in the next 10 years, the dual-engine models will account for 50%, the spare parts ratio will be 1.2, and the full-cycle replacement rate will be 1.8. The demand for aviation engines exceeds 3,240 units, and the market space for single crystal blades is about 102 billion yuan.
3.4.3. Derivatives The broad derivatives market is equally broad. Aeroengine blade and alloy technology can be derived into gas turbines and is widely used in power stations and ships. China's planned installed capacity of gas turbines in 2020 reached 120 million kilowatts, an increase of about 70 million kilowatts compared with the installed capacity at the end of 2014. According to the calculation of the mainstream 200 MW output of the gas turbine, the total installed capacity of the gas turbine exceeds 350 units. Compared with the traditional power, the gas turbine has the advantages of compact structure, high power, light weight and long service life, which can significantly improve the tactical technical performance of the ship. At present, there are only about 10 main ships in China that use gas engines. With the breakthrough of domestic marine gas turbine technology and the acceleration of naval ship loading speed, it is expected to form three major offshore fleets and several aircraft carrier formations in the future. In the next five years, it is expected to add about 30 destroyers and frigates, and 90 small and medium-sized ships. .

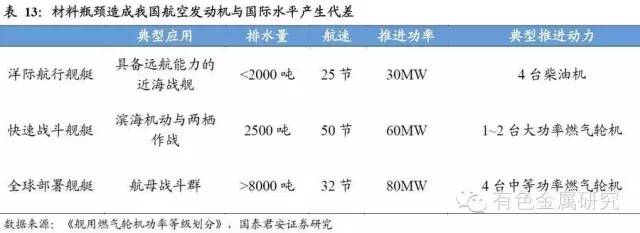
3.5. 3D printing meets the needs of aerospace widgets 3D additive printing technology has a technical foundation that is widely used in the aerospace industry. From the perspective of foreign 3D printing applications, the two major passenger aircraft manufacturers Boeing and Airbus have used 3D printing to manufacture titanium alloy parts on their latest models. Among them, Boeing revealed that it has established a 3D printing database consisting of a model database-parts management system-printer to produce related parts. From 1997 to 2015, more than 20,000 aircraft parts have been printed. Airbus has applied more than 1,000 3D printing components on the A350 XWB model. On the engine side, GE's compressor temperature sensor housing manufactured using 3D printing has passed the FAA airworthiness certification, and Rolla's bearing base parts manufactured using 3D printing have been used for the A380 and completed the test flight. It can be seen that 3D additive printing is widely used in aircraft part connectors and structural parts, and conventional forgings can be widely replaced.
Use 3D printing to increase aircraft manufacturing efficiency and reduce operating costs. Due to the large number of non-standard parts and consumables in the aircraft, individual manufacturing molds tend to be costly during the production process. In some connected parts and special parts with relatively low precision requirements, 3D printing can greatly improve production efficiency. For example, Rollo disclosed that the efficiency of using 3D printed parts can be increased by 1/3 and the lead time can be reduced by 30%. 3D printing will re-engineer the aviation material maintenance system to save operating costs. Due to the wide variety of aircraft parts and the high frequency of repairs, aircraft manufacturers and airlines have to bear a large inventory of spare parts in the maintenance of aircraft parts, and the spare parts delivery cycle is longer. In Boeing, for example, the number of parts purchased per year is 783 million, and there are 5,400 parts suppliers worldwide. 3D printing is expected to re-engineer the aerospace parts supply process. Some small parts will no longer be purchased by suppliers but directly by 3D printing, which is expected to significantly reduce inventory costs and shorten lead times.
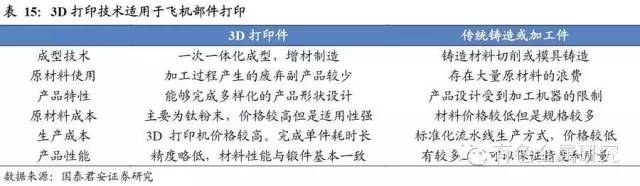
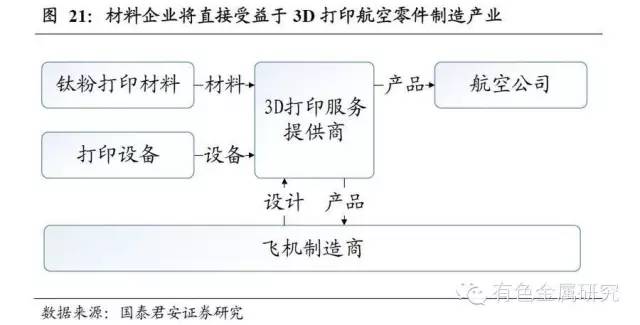
1) In the 1970s, it was mainly used for non-load-bearing structures such as fairings and hatches; 1 kg of CFRP could replace 3 kg of aluminum alloy;
2) In the 1980s, it was mainly used for secondary bearing structures such as vertical tail, flat tail, duck wing and auxiliary flap rudder surface, and the size and bearing capacity were further expanded;
3) In the 1990s, mainly with the maturity of the autoclave integral molding technology, CFRP was applied to large parts, including the fuselage and the wing. At the same time, the CFRP flaw detection technology has gradually matured and began to be applied in civil aviation aircraft;
4) Since 2010, CFRP has been tried to be used for engine fans. Due to the multi-layer cross-laying of the fibers, the material itself has an "anisotropic" performance, crack growth is slow, and the vibration attenuation rate is 5-6 times faster than that of the titanium alloy. The LEAP-X engine uses a CFRP three-dimensional carbon fiber braid to form a fan that achieves a fan weight reduction of approximately 50%.
3.6.2. Carbon-carbon composite materials: mainly used in brakes and have been applied to brake friction materials such as aviation and automobiles on a large scale. Carbon-carbon composites are lighter in weight, only about one-third of metal-based composites, and can be used as a friction material for brakes to reduce weight by 40%. At the same time, the material has good thermal stability. On the one hand, it has a good heat absorption function compared with high heat. On the other hand, it is not easy to melt and bond at a high temperature of 2000 degrees or above, which greatly reduces the maintenance frequency of aviation brakes. At the same time, the carbon-carbon composite material has certain structural properties, which helps to simplify the structure of the brake. At present, carbon-carbon composite materials have been widely used in the brake components of civil aviation and military aircraft, and gradually extended to friction materials such as automobiles and high-speed rail brakes.
3.6.3. Ceramic-based materials: Potential hot-end stator materials are primarily used to replace the stator material at the hot end of the engine. Ceramic matrix composites (CMC) may be the next generation of engine high temperature materials. Since the CMC weighs only one-third of the equivalent volume of metal alloy, the associated load-bearing components can be thinned, reducing engine weight and improving fuel efficiency. At the same time, the operating temperature of CMC is about 500 degrees higher than that of nickel-based alloy, which can greatly increase the operating temperature of the hot end and reduce the air-cooled components and design (the secondary turbine does not even need air cooling). When fully applied, the engine can be reduced by about 6% (455 kg).
At present, CFM's latest LEAP engine uses CMC material as the high-pressure turbine casing, and the GE9X will further expand the CMC range to the inner and outer combustor liners, high-pressure turbines 1 and 2 nozzles (static vanes), and 1 Stage shroud.
3.6.4. Porous Metal Film (EMF)
Mainly used for lightning protection of composite fuselage. Aircraft anti-light has become an important issue due to the large replacement of aluminum alloy fuselage in the fuselage. In aircraft manufacturing, the protection of composite fuselage lightning protection mainly uses porous metal foil (EMF).
In short, the development of many fields of aviation materials has greatly promoted the rapid development of related fields. Universities, research institutes and enterprises can jointly promote the import substitution of aviation materials. China's industry prospects in the aviation field are very broad.
Material :Natural slate , quartz,sandstone ,marble etc .
Size :12''*12'',16''*16"",24''*24'' etc .Can also be made as your requirement
Shape :Rectangle ,square shape etc.
Packing :Hard carton then fumigated strong wooden crate.
The wooden crate size is made as the container size . After loading the wooden crate in the container ,the wooden crates will nearly same size with the width of the container .It can make the wooden crate not have space to move during transport . In this case ,it can keep the stone safety mostly
Application : Can be used to decorate the outside wall or inside wall .Decorate your house ,decorate your life .
Slate Tiles,Slate Floor Tiles,Slate Wall Tiles,Outdoor Slate Tile
HEBEI DFL STONE , https://www.dflstone.com