I. General overview
Leakage is a common phenomenon of injection molding machines, mainly due to the pressure difference caused by the flow of liquid in the hydraulic components and pipelines and the gap between the components. In addition, the harsh working conditions will also have a certain impact on the sealing of the injection molding machine. Once the hydraulic system leaks, it will cause the system pressure to fail to build up. The hydraulic oil leakage will also cause environmental pollution, affecting production and even producing unpredictable serious consequences. The following is a brief discussion of the causes of leakage and countermeasures for some factors that affect the leakage of the hydraulic system of the injection molding machine.
Second, the classification of leaks
There are two main types of leakage in the hydraulic system of the injection molding machine. Leakage at the fixed seal and leakage at the moving seal. The leakage at the fixed seal mainly includes the bottom of the cylinder and the joint of each joint. The movement seal mainly includes the piston rod of the cylinder. Multi-way valve stem and other parts. From the leakage of oil, it can also be divided into external leakage and internal leakage. The external leakage mainly refers to the leakage of hydraulic oil from the system to the environment. The internal leakage refers to the existence of the pressure difference between the high and low pressure sides and the failure of the seal. The hydraulic oil flows from the high pressure side to the low pressure side inside the system.
Third, the reasons for the impact of leakage
(1) Design factors
(1) Selection of seals
The reliability of the hydraulic system depends to a large extent on the design of the hydraulic system seal and the choice of seals. Due to the unreasonable selection of the seal structure in the design, the selection of the seal is not standardized, and the hydraulic oil is not considered in the design. The compatibility type of the sealing material, the load condition, the ultimate pressure, the working speed, the change of the ambient temperature, and the like. These all directly or indirectly cause hydraulic system leakage to varying degrees. In addition, since the environment of the injection molding machine has dust and impurities, a suitable dustproof seal should be selected in the design to prevent dust and other contaminants from entering the system to damage the seal and contaminate the oil, thereby causing leakage.
(2) Other design reasons
The design takes into account the geometric accuracy and roughness of the moving surface is not comprehensive and the strength check of the joint is not carried out in the design, which will cause leakage in the mechanical work.
(2) Manufacturing and assembly factors
(1) Manufacturing factors
All hydraulic components and sealing components have strict dimensional tolerances, surface finishes, surface finishes and dimensional tolerances. If the manufacturing process is out of tolerance, for example: the piston radius of the cylinder, the depth or width of the sealing groove, the hole size of the sealing ring is too poor, or the machining is caused by the problem of rounding, burrs or defects, chrome peeling, etc. The piece will be deformed, scratched, crushed, or pinched, causing it to lose its sealing function. The part itself will have a congenital point of leakage, which will leak after assembly or during use.
(2) Assembly factors
Hydraulic components should be eliminated from rough operation during assembly. If excessive force is applied, the parts will be deformed, especially with copper rods, etc.; the parts should be carefully inspected before assembly, and the parts should be slightly hydraulic when assembled. Oil, gently press in, use diesel oil during cleaning, especially rubber components such as seal ring, dust ring, O-ring, etc. If you use gasoline, it will easily age and lose its original elasticity, thus losing the sealing function.
(3) Oil pollution and damage to parts
(1) Gas pollution
At atmospheric pressure, about 10% of the air can be dissolved in the hydraulic oil. Under the high pressure of the hydraulic system, more air or gas is dissolved in the oil. The air forms bubbles in the oil. If the hydraulic support changes rapidly between high and low pressure in the short time during the working process, the bubble will generate high temperature on the high pressure side and burst on the low pressure side if the components of the hydraulic system When there are pits and damage on the surface, the hydraulic oil will rush toward the surface of the component to accelerate the wear of the surface, causing leakage.
(2) Particle pollution
Hydraulic cylinders are the main actuators of some hydraulic systems of injection molding machines. Due to the exposed piston rods in the working process, they are directly in contact with the environment. Although dustproof rings and seals are installed on the guide sleeves, dust and dirt are inevitable. Into the hydraulic system, accelerate the scratches and wear of seals and piston rods, causing leakage, and particle contamination is one of the fastest factors for hydraulic component damage.
(3) Water pollution
Due to factors such as dampness of the working environment, water may enter the hydraulic system. Water reacts with the hydraulic oil to form acidic substances and sludge, which reduces the lubricating performance of the hydraulic oil and accelerates the wear of the components. The water also causes the valve of the control valve. The rod is bonded, making it difficult to manipulate the valve to scratch the seal and cause leakage.
(4) Part damage
The seal is made of oil-resistant rubber and other materials, which may cause system leakage due to aging, cracking, damage, etc. due to prolonged use. If the part is damaged by a collision during work, it will scratch the sealing element and cause a leak.
Fourth, the main prevention and control measures
The factors that cause the leakage of the hydraulic system of the injection molding machine are the result of various comprehensive effects. With the existing technology and materials, it is very difficult to fundamentally eliminate the leakage of the hydraulic system of the injection molding machine. Only from the above factors affecting the leakage of the hydraulic system, take reasonable measures to minimize the leakage of the hydraulic system. In the design and processing steps, the design and processing of the sealing groove, which is an important factor affecting the leakage, should be fully considered. In addition, the choice of seals is also very important. If the factors of leakage are not fully considered at the beginning, it will bring immeasurable losses to future production. Choose the right assembly and repair methods and learn from past experience. For example, use special tools in the assembly of the seal and apply some grease to the seal. In the control of pollution of hydraulic oil, it is necessary to start from the source of pollution, strengthen the control of pollution sources, and also take effective filtration measures and regular oil quality inspection. In order to effectively cut off the pollution of hydraulic cylinders by external factors (water, dust, particles, etc.), some protective measures may be added. In short, the prevention and control of leakage must be comprehensive, and comprehensive consideration can be effective.
Calcium Chloride Description :
Calcium chloride is an inorganic salt, which exists as solid or liquid. Solid calcium chloride is a white, crystal substance in the form of flake, granule, pellet or powder. With different crystallized water contents, it can be dihydrate or anhydrous. Liquid calcium chloride is a colorless, clear solution. As calcium chloride has such properties as quick dissolving, exothermic ability, attracting moisture from the air and surroundings, dissolving at very low temperature
Calcium Chloride Application :
1. They are widely used in highway, expressway, parking lot and port to melting snow and ice.
2. Used as dryer, as anti-fog, and anti-dust agent also fireproof agent
3. Protective agent and refining agent for petroleum/oil field.
4. Pigment assistance agent of textile. It is a kind of raw material.
5. It acts as flocculation in Water treatment.
6. Be used in waste paper processing as removing printing ink agent.
7. As anti-freezing agent.
8. As dehydration agent.
9. Food additive: as cryogen are used in ice cream, as stable agent/coagulant used in bean products, drink and beer.
94% calcium chloride pellet
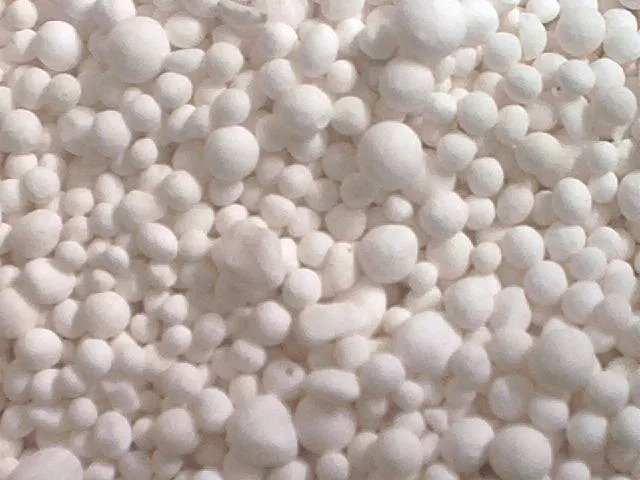
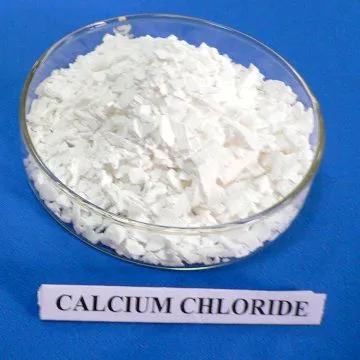
Calcium Chloride Specification
Item |
Standard |
|
74% Flakes/Granular |
77% Flakes/Granular |
|
Calcium chloride as CaCl2 |
≥74% |
≥77% |
Total alkali chloride as NaCl |
≤7.0% |
≤5.0% |
Total magnesium as Mgci2 |
≤0.5% |
≤0.5% |
Alkalinity as Ca(OH)2 |
≤0.4% |
≤0.4% |
Insoluble in water |
≤0.3% |
≤0.2% |
Item |
Standard |
|
94% Prills |
94% Powder |
|
Calcium chloride |
≥94.0% | ≥94.0% |
Magnesium and alkali chloride(NaCl) |
≤5.5% | ≤3.5% |
Water insolubles |
≤0.2% | ≤0.2% |
Alkalinity[Ca(OH)2] |
≤0.35% | ≤0.3% |
Sulfate(CaSO4) |
≤0.2% |
≤0.2% |
FE |
≤0.1% |
≤0.1% |
Calcium Chloride Package
25KG/ 1000KG PP woven bag
Calcium Chloride
Calcium Chloride,Calcium Chloride Flakes,Calcium Chloride Pellets,Calcium Chloride Dihydrate
Shandong Tiancheng Chemical Co., Ltd. , https://www.tianchengchemical.com